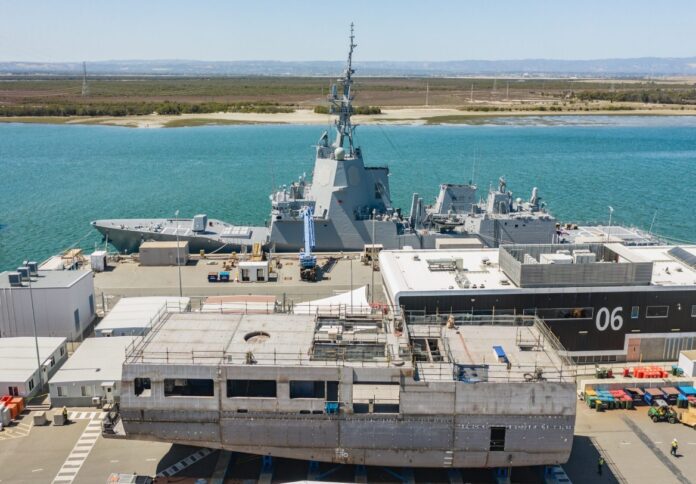
BAE Systems Australia has completed the weeklong trials of a new laser scanning technology that can create 3D models of pipes found on the Hunter class frigate.
Conducted at the Osborne Naval Shipyard and Henderson shipyard, the trials demonstrated the technology’s capabilities in a real manufacturing environment.
The trials were conducted following initial testing at the Line Zero – Factory of the Future facility in Adelaide’s south and BAE Systems Australia’s Henderson shipyard.
BAE Systems’ teams involved in the trial have identified potential efficiencies in time spent checking the product quality produced by specialist pipe bending equipment.
Each Hunter class frigate requires thousands of pipes with unique dimensions. Using a hand-held scanner, engineers can scan the pipes and create a 3D model in just five minutes. The equipment and software are precise up to 100 to 200 microns.
According to BAE Sytems, the trials showcased the technology’s capabilities to streamline production processes on the Hunter program, as well as its potential to support the sustainment of Australia’s existing fleet of warships with the capability to reverse engineer, produce and replace pipes and connecting pipework.
“We are working with cutting-edge technology to drive as much efficiency as possible in the shipyard,” said Sharon Wilson, BAE Systems Australia’s Business Development and Continuous Naval Shipbuilding Director.
“This is yet another example of adapting commercially available equipment, which we have tested in the open environment at Line Zero – Factory of the Future, for use in the shipyard.”
“The insights gained from these trials have huge benefits not only for our Hunter Class Frigate Program and the Anzac Midlife Capability Assurance Program, which we are delivering with our partners in the Warship Asset Management Agreement but also for continuous naval shipbuilding here in Australia,” Wilson added.