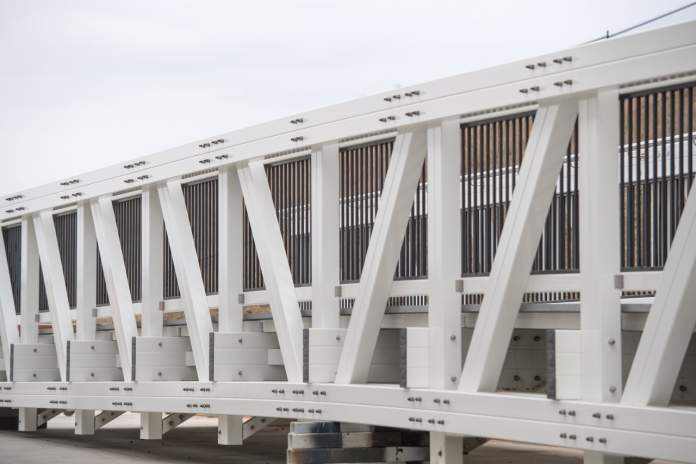
Media Release
Material designed and developed in Toowoomba, Queensland is being used in multi-million dollar projects around the world, including a two-kilometre boardwalk in Abu Dhabi.
‘Pultrusion’ is the next big thing in manufacturing, and Wagners Composite Fibre Technologies (CFT) have teamed up with the University of Southern Queensland (USQ) and Allnex to redefine what the manufacturing process is capable of.
USQ Polymer Composites researcher Dr Xuesen Zeng said pultrusion created continuous lengths of composite material, ‘pulling’ fibre-reinforced profiles through a cross-section of die, resin and heating and cooling zones.
“It has been the manufacturing method of choice due to its ability to produce large sections in volume which are economical and consistent in quality,” Dr Zeng said.
“We’re increasing the productivity of the process, incorporating additives such as fire retardants, integrating braiding process with pultrusion, optimising injectable tools, and more.”
USQ, Wagners CFT and Allnex have embarked on a $10 million project that recently received a $3 million funding boost from Australian Government’s Cooperative Research Centres (CRC) program.
Together they are creating advanced structures expected to capture new high value markets in the oil and gas and transport industries both in Australia and internationally.
Wagners CFT is a pioneer in the use of composite materials in civil engineering around the world with projects using pultruded material in the UK, USA, and New Zealand.
They are currently in the process of installing a boardwalk for the United Arab Emirates’ AL Jubail Island Development which will see 6,000 villas constructed on the island.
USQ Institute for Advanced Engineering and Space Sciences Executive Director Professor Peter Schubel said investment by USQ in a production-ready Pultrex pultrusion line has allowed USQ to operate as the research arm of Wagners CFT, freeing up precious production time, leading to the development of new products in new markets with improved mechanical and fire performance.
“The integration of experimental and modelling capabilities will help increase productivity through higher line speed, and create structures that can compete on cost within Australia and in the global market,” Professor Schubel said.
USQ is recognised worldwide for its track record in implementing research and development projects in automated fibre composites for civil infrastructure. USQ has industry relevant manufacturing facilities, material characterisation and structural testing facilities for research and commercial testing.
Image Credit: Image Provided