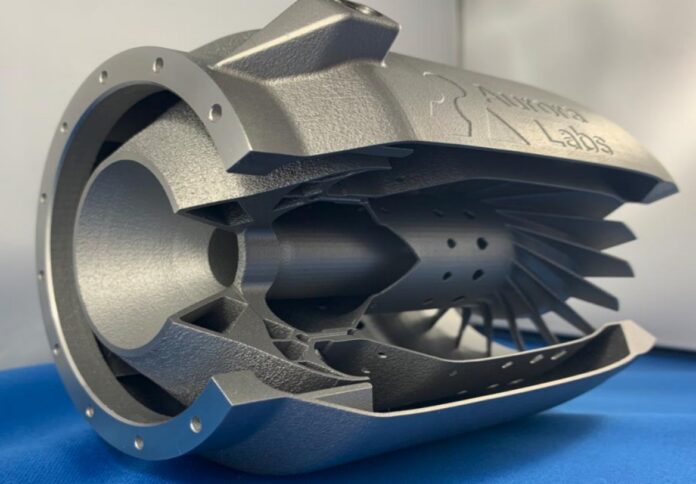
Aurora Labs Limited (A3D) is set to present a 3D metal-printed gas turbine component at the IndoPac Maritime Conference in Sydney this week, geared towards defence customers and manufacturers.
The gas turbine component on display, measuring 130mm in outside diameter and standing 150mm tall, showcases the extraordinary capabilities of A3D’s laser powder bed fusion machine, a system designed and constructed by the A3D team.
According to the ASX-listed company, the gas turbine component chosen for display has garnered acclaim within the additive manufacturing industry for its technical complexity.
It boasts numerous intricate channels and through-holes that must be printed without the need for additional support structures. Furthermore, the part must be entirely free of residual powder upon removal from the build chamber.
The component also incorporates various sharp angles and overhangs, an industry term describing sections of a component that lack support from underlying layers and are characterised by their overhang angle and height.
One of the key advantages of this cutting-edge technology is its rapid design, manufacturing, and preparation process.
In a matter of just a few days, A3D can create a gas turbine component, which is a significant advantage in defence applications where supply chain delays are largely unacceptable.
Gas turbines are known for their high power-to-weight ratio and can be easily customised or simplified through AM design processes. This makes them ideal for use in defence applications.
Their geometry can be printed rapidly as a small number of components, a feat that traditional manufacturing methods cannot easily replicate.
The company said traditional methods typically involve machining in multiple stages, while 3D printing allows for the entire component to be created in a single print.
These turbines can be printed using various corrosion-resistant materials or specialised materials to address concerns related to fatigue and heat.
This ensures that they can withstand extended operational hours and combat issues such as corrosion, creep, or cracking.
CEO Rebekah Letheby expressed her excitement, saying, “The successful printing of such complex features is a testament to the Team’s expertise.”
“It shows our customers that we have a machine capable of printing at a high level of technical difficulty and that they can rely on an Aurora machine to do such demanding work, meeting quality specifications,” the CEO added.
Aurora anticipates numerous conversations with interested parties at the IndoPac Conference regarding this category of printing.