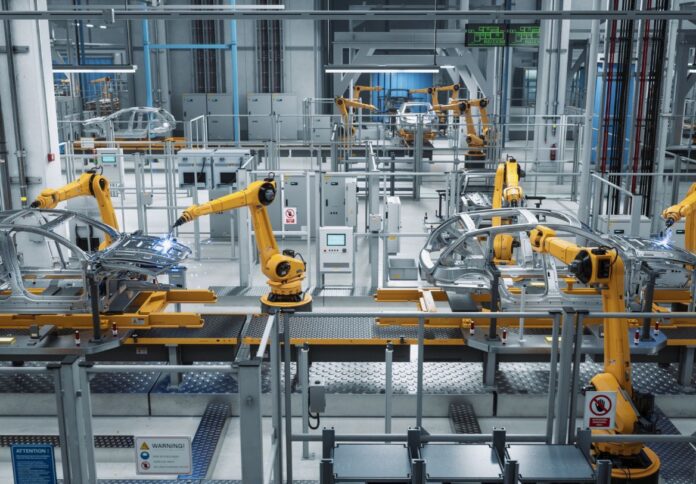
Following its successful virtual discussion in December 2022, leading NetSuite implementation partner Annexa is facilitating yet another exchange of insights and ideas aimed at building an efficient and resilient manufacturing operation in Australia.
On 14 February, Annexa’s latest webinar “Combating Warehouse Inefficiencies With RF-SMART + NetSuite” will focus on transforming warehouse solutions and will feature RF-SMART, a global leader in mobile data collection solutions for supply chain/logistics execution.
Developing operational and supply chain resilience has been one of the top priorities of manufacturers as they face various headwinds such as market volatility.
In its previous webinar, Annexa and major homewares brand Linen House shared how transforming operations with cloud enterprise resource planning can help business leaders stay agile and competitive in an uncertain economic environment.
The webinar, titled “Building a Resilient Manufacturing Future,” featured Tex Osman, information technology director at Linen House, and Matthew Owens, director of sales and marketing at Annexa.
Osman dove into the strategies and capabilities of cloud ERP leveraged by Linen House in a bid to optimise inventory and warehouse management, allowing the company to better navigate global supply chain instability.
Streamlining shop floor processes
According to Osman, implementing NetSuite as the single source of truth helped address the need for a system that spoke to all the different peripheral business units Linen House runs.
The business needed an ERP system that is equipped with all the mechanics to manage the inventory, not just for wholesale, but for retail outlets as well.
Osman highlighted the two capabilities that NetSuite has made possible for managing Linen House’s massive inventory—verification and end-to-end product information workflow.
Verification is a crucial component in NetSuite, Osman noted, as it essentially automates processes, allowing the business to manage all the inventory in an accurate way across all the different business units.
“That is of the one key factors as a business like ours now relies on the accuracy of the stock across all those channels. You can’t be making too many mistakes otherwise your shops have no stock or your website can’t fulfil orders.”
Product information workflow, according to Osman, is essentially the technology within NetSuite that enables a complete end-to-end product lifecycle management, starting from product inception, design, sourcing of materials, all the way through to manufacturing, pricing and putting it up on the website for selling.
“The entire lifecycle of that product lives within that product information development— that programming,” Osman said.
Registrations for Annexa’s latest webinar can be completed here.
To watch Annexa’s previous virtual discussion on demand, register at info.annexa.com.au.