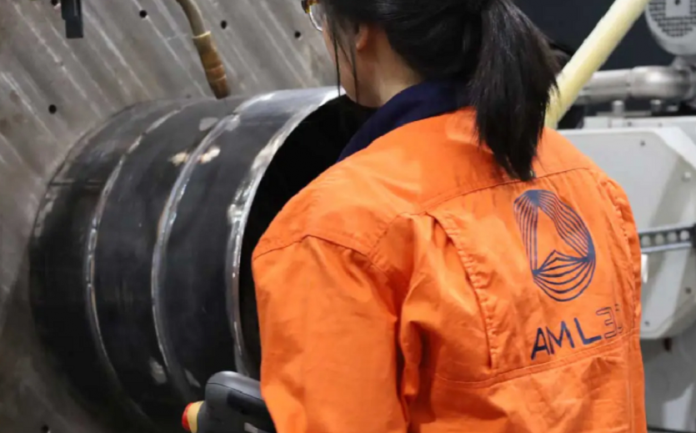
3D metal printing company AML3D has partnered with Deakin University’s Institute for Frontier Materials (IFM) to develop high strength wire feedstock alloys suitable for high strength applications.
Currently operating out of its Adelaide Manufacturing Centre, AML3D provides commercial large-scale “additive metal layering” 3D printing services to defence, maritime, automotive and resources customers using its patented WAM process.
According to the company’s statement, the partnership with IFM will predominantly focus on optimising technology for high strength alloys, such as wire feedstock for 3D printing and welding markets.
“The partnership will support specific design of alloys that will deliver high strength wire coil for printing, with no need for subsequent post processing,” reads the statement.
AML3D Managing Director Andrew Sales, said the partnership would open up new markets and applications for WAM, such as maintenance and repair tasks where WAM can be directly applied to existing vehicles and structures.
He said the company has also identified additional alloy development opportunities with commercial outcomes, which will be scoped separately under the agreement.
“The successful development of these alternative alloys provides significant potential upside for our business, not only through its application in WAM and providing for other wire-fed DED processes, but the sales as a standalone feedstock product with widespread applications,” Mr Sales continued.
“The intended production of wire feedstock will provide an alternative within the general welding technology market that exceeds current applications.
“Whilst application through WAM will provide customers greater flexibility in their choice of metal alloys, further enhancing the market leading position of our technology.”
Andrew Rau, Senior Commercial Manager at Deakin University added: “IFM has a long and proud history of partnering with industry to deliver applied research leading to commercial outcomes.
“This exciting partnership with AML3D is perfectly aligned with the unique facilities and capabilities within IFM and collectively we are looking forward to developing a range of unique alloy solutions enabling AML3D to continue to expand the markets and applications for their patented WAM additive manufacturing process.”