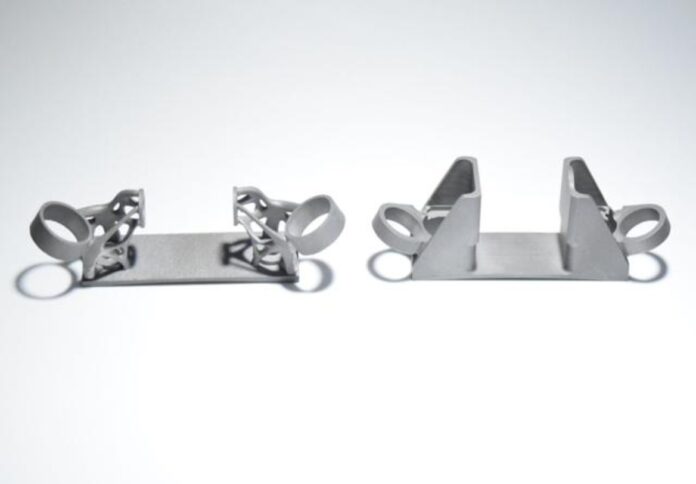
Collaborations across the additive manufacturing industry are paving the way to address the demand for more sustainable manufacturing as well as more robust and flexible supply chains in a strategically, financially, and environmentally beneficial way.
The Additive Manufacturer Green Trade Association (AMGTA), the first and only organisation devoted to 3D printing sustainability, brings together the manufacturing and sustainability industries to better grasp the AM leveraging potential through its first independent study.
Commissioned by the AMGTA and authored by the Rochester Institute of Technology’s Golisano Institute of Sustainability, the study, titled, “Comparative LCA of a Low-Pressure Turbine (LPT) Bracket by Two Manufacturing Methods,”, analysed a commercial aerospace low-pressure turbine bracket.
This was done through a life cycle assessment (LCA), evaluating both the comparative manufacturing impact of laser powder bed fusion (LPBF) AM vs traditional manufacturing of the bracket and the effect of a greater than 50 per cent weight reduction of the bracket over the life of the aircraft.
Ultimately, the study was unable to identify which manufacturing method consumed the most energy, but it did indicate that lightweighting commercial aircraft engines and airframes have a significant impact on carbon emissions.
The additive design and manufacturing of the bracket
The bracket under consideration was one of 12 designed to secure fuel manifolds to the external casings of the low-pressure turbine modules of two GE Aviation CF6-80C2B6F turbine engines mounted on a Boeing 767.
The part, chosen for its simplicity and ease of access, was redesigned for additive and printed on an EOS M290 3D printer with Höganäs AB Inconel 718 powder by AMGTA member Sintavia. Meanwhile, a Tennessee-based machine company CNC’d the traditional counterpart.
According to Sintavia, the redesigned AM bracket weighed 50 per cent less, or 0.063 kg, than the original version while exhibiting improved mechanical qualities, including extended fatigue life.
Inconclusive on the manufacturing method
The LCA employed three different methodologies, but it was unable to determine whether traditional or additive manufacturing methods consumed more energy.
Overall, this result was neutral, which was an improvement over earlier research that indicated LPBF manufacturing required more energy than conventional methods, according to the study.
Significance of energy mix
The study discovered that the energy mix of a manufacturing plant at the place of generation, as well as whether that energy grid was produced through sustainable means, was by far the most important element in influencing production sustainability.
Major effect on lightweight aircraft
The research clearly showed that using AM design for lightweight aircraft components resulted in a huge decrease in carbon emissions during the life of an aircraft, with a reduction of 13,376 kg for every 1 kg of weight reduction.
Overall, AM created a more sustainable part
By far the most important factor in deciding that AM-produced components are more sustainable than traditionally designed and manufactured parts were the influence of lightweighting.
According to the AMGTA, the inconclusive nature of the initial finding actually proved an improvement over prior, similar research that found AM to use more energy than traditional methods.
Two of the three LCA approaches stated that the traditional bracket used less energy to build, while the 3D-printed bracket produced fewer emissions.