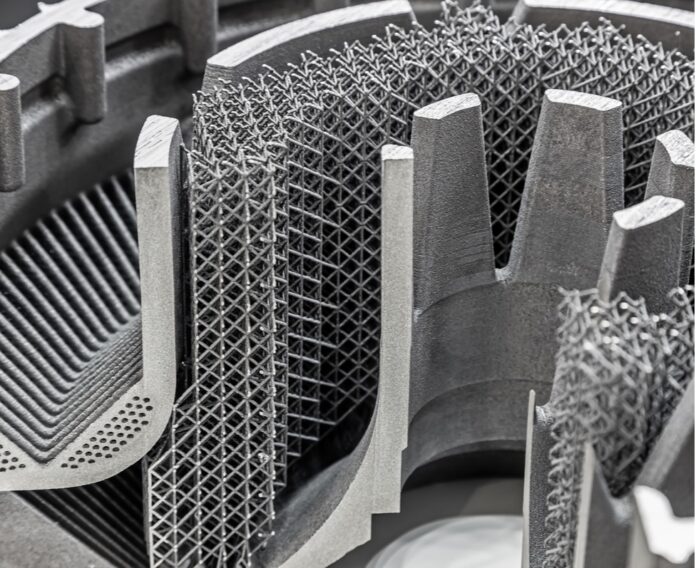
Colorado-based Alio Industries President Bill Hennessey said the company serves as a crucial one-stop-shop for all positioning requirements in AM applications, offering a comprehensive range of motion solutions.
He stated in a press release that Alio’s comprehensive portfolio, which includes XY-stages, 6D Hybrid Hexapods, gantries, and fully integrated motion solutions, responds to the unique needs of AM practitioners while simplifying the selection and integration process.
Hennessey also said that Alio streamlines procurement, ensures compatibility, and facilitates technical assistance by offering a single source for positioning components, eventually improving operational effectiveness and dependability for AM system developers and operators.
The Alio official further underscored how precise motion control systems play a crucial role in minimising errors, defects, and inconsistencies in the AM process.
“Any deviations or inaccuracies in the motion can lead to misalignment, overextrusion, or insufficient material deposition, compromising the integrity and quality of the printed parts,” he explained.
He said high-end motion control systems use cutting-edge feedback devices, including encoders or sensors, that give the control system real-time position feedback.
“This feedback enables closed-loop control, allowing for immediate adjustments and corrections during the printing process, thereby ensuring accurate and consistent deposition of material layer by layer,” Hennessey noted.
According to Alio, the need for accurate motion control systems grows dramatically when AM moves from a prototype to a production technique.
When prototyping, the emphasis is frequently on building workable proofs-of-concept or miniature models, where tolerances and accuracy standards may be more slack.
However, Alio argued that the demand for exact motion control increases as additive manufacturing develops into a production process.
“In production-scale AM, there is a higher demand for consistent and repeatable quality across large quantities of parts. Precise motion control ensures that each layer is accurately positioned, minimizing dimensional variations and maintaining the desired geometries throughout the production process,” the company explained in the press release.
Overall, according to the company, precise control over component motion enables faster deposition rates, decreased superfluous motions, and optimised path planning.