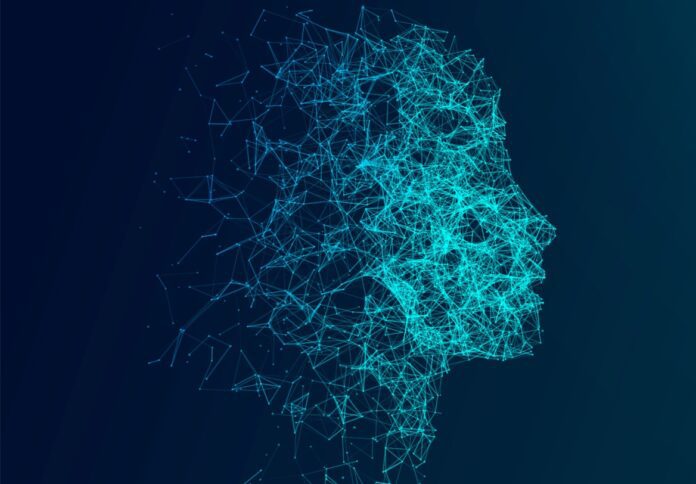
Article by Datacom’s Associate Directors for Futures + Insights Tracey Cotter-Martin and Industry Dave Ffowcs-Williams
If we distilled the common objectives for manufacturing in this country the priorities that surfaced would no doubt centre on greater productivity, more sustainable processes and the ability to keep pace with market leaders and be globally competitive.
AI is a great fit for this wish list.
One of the simplest ways to increase productivity is to minimise downtime. Manufacturers can use AI to monitor and analyse data from machinery and production processes to identify anomalous patterns and then proactively resolve issues before they result in breakdowns.
Optimisation is another AI strength. AI’s ability to quickly analyse large amounts of data and predict likely outcomes can be used to inform better decisions about supply chain, production lines, scheduling, product materials, reducing waste and to improve the accuracy of forecasting.
AI is also the ideal tool for QA. The tedium of testing and quality control is the perfect application of AI, which paired with sensors and image recognition software can be used to automatically detect equipment damage and product defects.
Some of the debates about AI seem poised to pit AI as an either-or scenario, with the implied threat that it will wholly replace existing teams and processes.
But AI’s sweet spot is augmenting smart teams and allowing organisations to adapt (and compete) by enabling lower risk experimentation at pace.
For example, the powerful pairing of a digital twin and AI allows a manufacturing team to accurately simulate changes to specific components or whole systems and then use the resulting data to predict future outcomes, model ‘what-if’ scenarios and refine processes. In this scenario, the team uses AI to pinpoint smart, better performing and more cost-efficient processes, without having to go through disruptive trial-and-error testing.
With these examples in mind, rather than viewing AI as a threat, we hope AI can be considered as a potential ace in the hole for Australian manufacturers. The stats show there is already a strong global push: according to estimates, the global AI in manufacturing market was valued at $3.2 billion in 2023 and is poised to grow to $20.8 billion by 2028.
But before you rush in, there are a few provisos.
First steps on the road to AI
Any organisation looking to implement AI needs to focus on getting the foundations right. One of the critical foundations is having the right reason – don’t adopt AI for the sake of it. Think about the problem you need to solve and how AI can help play a role in the solution.
Implement some AI guardrails at the outset. Research carried out by Datacom last year showed the adoption of AI is outpacing the introduction of policies for AI use. Think about acceptable, ethical uses of AI in your business – and of the data that will be feeding your AI tools and being generated – and develop guidelines your team can follow.
Get familiar with the AI options that exist or enlist help to understand them. Right now a number of major players are vying to come out as the leaders in AI, but setting aside this popularity contest it can be helpful to understand the two major flavours of AI: machine learning (ML) and large language models (LLMs). ML has been around for a comparatively long time and works well with structured data and existing, readily available algorithms. LLMs are the ones making headlines because they can cope with human language and less structured data, but the quality of the output relies heavily on the quality of the input and language rules. ML could be a better place to start for manufacturers, but both flavours of AI require careful planning and change management.
The relationship between inputs and outputs is probably more keenly understood by an AMA audience than most, but if you’re implementing AI then you must have your data and your supply chain in order first. If you’re using bad data, the AI being fed that data can’t deliver good results, and if your supply chain isn’t straight then the downstream effects of introducing AI will be unpredictable.
AI holds massive potential to contribute to more sustainable, more productive manufacturing in Australia, but the focus needs to be on augmenting not replacing – and we all need to get the foundations right first.