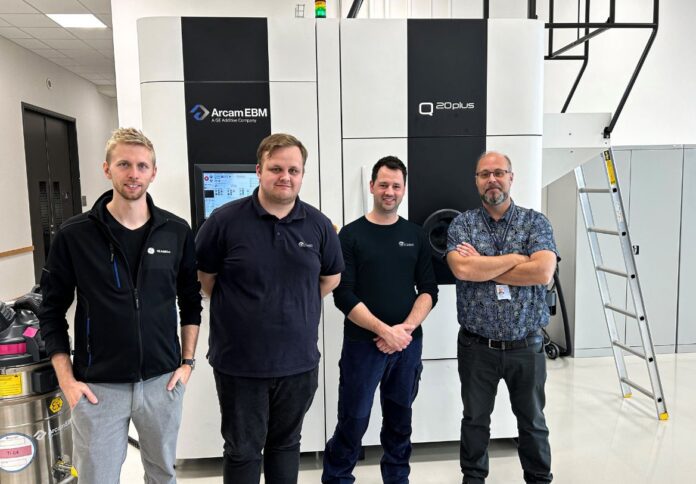
A new advanced manufacturing facility that will build more durable satellites and hypersonic structures is underway in Adelaide as part of the first Innovative Launch, Automation, Novel Materials, Communications and Hypersonics (iLAuNCH) Trailblazer project.
Set to be located in proximity to space sector businesses in South Australia, the upcoming facility will design and manufacture stronger satellite and hypersonic vehicle structures using additive manufacturing.
The iLAuNCH Trailblazer program includes partners such as the Future Industries Institute at the University of South Australia (UniSA) and Adelaide-based advanced manufacturer VPG Innovation.
Professor Colin Hall of UniSA said the upcoming iLAuNCH hub will be dedicated to building the space engineering capability of the Australian manufacturing sector.
“This project, the first to kick off for the space trailblazer program, will deliver additive manufacturing, at scale to Australia,” Hall said.
The partnership intends to support a world-class Australian sovereign manufacturing capability that will create new jobs alongside a highly trained workforce, leading to global exports within the space industry and other markets, according to Darin Lovett, executive director of iLAuNCH Trailblazer.
Leveraging UniSA’s established additive manufacturing capability, the project will support an increase of VPG employees and the upskilling of current ones in the area of AM for space applications.
The initiative will also use additive manufacturing technology through Electron Beam Melting (EBM) of metals, a technique in which almost all of the energy put into creating the electron beam goes into melting the metallic dust.
The EBM process takes place in a vacuum, allowing for a high temperature in a non-oxygenated environment, which relieves internal stresses and results in more resilient flexible parts.
The additive manufacturing method removes limitations imposed by traditional manufacturing approaches, providing designers of space objects with opportunities to optimise parts for performance.
“The project is full steam ahead; we already have two engineers in Sweden developing the practical skills to operate and maintain the systems. It’s great to work with a company, that is innovative, proactive and has a long-term vision,” according to Professor Hall.