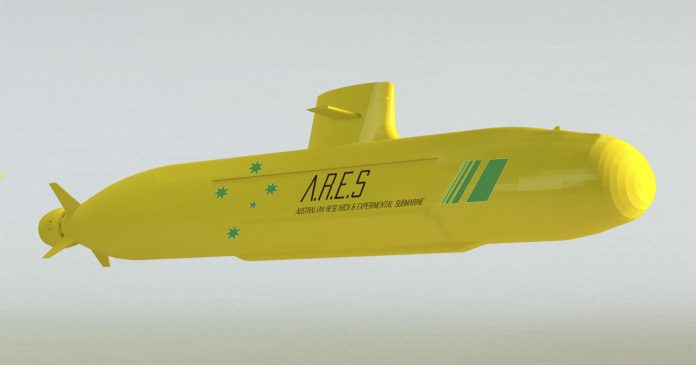
Media Release
A three-year project to design, manufacture and test Australia’s first yellow submarine will begin next month.
The fully reconfigurable Australian Research Experimental Submarine (ARES) will be used for hydrodynamic and crew efficiency testing of future submarine designs.
A full business case is still being finalised ahead of the kick-off meeting in Adelaide, South Australia, in February.
The project is collaboration between the University of Adelaide, University of South Australia, Flinders University, TAFE SA and the University of Tasmania’s Australian Maritime College with Defence support from DST Group.
The four industry partners for the project are SAAB, ASC, Dassault Systemes and MOOG Australia.
ARES received $150,000 in Defence Innovation Partnership funding from the South Australian Government last month to boost a $350,000 in kind contribution from participants to fund the project’s first year. An estimated $3 million will be needed to complete the three-year project.
Project lead and University of Adelaide Director of the Shipbuilding Hub for Integrated Engineering and Local Design (SHIELD) Eric Fusil said the project would deliver Australia’s first reconfigurable research submarine.
He said the autonomous submarine would be used to test hydrodynamics – how a submarine behaves underwater – to aid in the design and safe operation of new submarines globally.
“Because you can’t see on board a submarine and you don’t really know where you are going, you need to know that when you are pulling on the controls from inside the submarine that you are setting the control planes outside at a given angle.
“You need to know the effect of these angles for each given speed on the trajectory of the submarine – otherwise you are at risk of breaching the surface or diving too quickly.
“Despite all our best efforts worldwide we’re still at a point where we cannot use computers to predict all of that. You need to go to actual testing with small-scale submarines to be able to deliver a safe analysis of how present or future submarines are behaving underwater.
“These vehicles are often quite specific to a class of submarine whereas our submarine will have the ability to be generic and to be adaptable to any kind of shape overall and also to any kind of location of contour plane.”
Early designs show the submarine to be about 7-metres long and up to 1.8m high. Its ‘golden wattle’ yellow colour will allow it to be easily observed during underwater tests.
Initial testing will likely be done in lakes at a depth of 30-40m – deep enough to properly test the submarine’s hydrodynamics but shallow enough for it to be safely recovered by dive teams if it encounters problems.
While Australia has not previously had a research experimental submarine, several of its allies including the United States, United Kingdom, The Netherlands and France have used them extensively.
Fusil said the project would also help develop a skilled workforce that will go on to contribute to Australia’s future submarine program.
“The project is quite unique because in Australia so far we have taken products off the shelf and we have customised and adapted them to our Australian environment,” he said.
“On this project we are starting pretty much from scratch but we have access to a very good technical support network including UK, The Netherlands and potentially the French so we will be able to feed on the lessons learned from these countries and take the best from all of them to build a successful model.”
The project will also enlist the help of several international ‘Grey Beards’, experienced industry experts who will mentor and guide the project.
The first year of the project will mainly involve design work before procurement, manufacture and testing phases in years two and three.
South Australia is pivotal in Australia’s $50 billion plan to regenerate the Royal Australian Navy, including 12 Attack Class submarines to be built at the Osborne Naval Shipyard in Adelaide, which is undergoing a $500 million upgrade.
Dassault Systemes will provide its 3DExperience software platform, which is likely to be the environment in which Australia’s future submarines are developed.
Fusil said the 3D Experience software would cover the full cycle of engineering and production from the very early stages of design through to the transition to procurement, manufacturing and testing.
“The 3D Experience will integrate Industry 4.0 aspects and enable us to cover the whole life-cycle from design to test and activation and that’s a big challenge that nobody has done before,” he said.
“It is definitely the ambition – not just in defence but industry overall – to go fully digital and Dassault’s 3D Experience is a product that claims that to be completely possible.”
Fusil said DST Group – the Australian government’s Defence Science Technology agency and one of the project’s major partners – would have the opportunity to use ARES to help develop the Attack Class submarine and also to validate other projects Australia is involved in with its allies.
“Our aim – because we are universities with industries and DST – is to start with an unclassified submarine shape but we want that shape to be able to be used by our sponsors such as DST for classified testing if they elect that to be the case,” he said.
“But we are also aware there is a niche market for these vehicles.
“Because submarines are being considered by many navies including in the Southeast Asian region, there are a number of countries that are interested in accessing this kind of technology.
“We could export that vehicle because it is based on an unclassified shape and it can be customised we could sell this kind of free-running model to our neighbouring countries interested in having their own model to be used for analysis to develop their own submarines.”
The project is one of four South Australian projects funded through the latest round of the Defence Innovation Partnership.
Defence SA Chief Executive Richard Price said South Australia’s three universities each had specific strengths in a range of defence-relevant fields,” Price said.
“We are applying this capability by connecting these researchers with our defence industry to accelerate development and build solutions to key projects for Australia,” he said.
“The importance of collaboration between defence industry and researchers cannot be understated; it is the foundation for success and key to solving increasingly complex Defence problems.”
Fusil said securing funding for years two and three was key to delivering the full project.
“We need to prove to the stakeholders that we are serious and that we are here to deliver.
“We’ve got interest from a number of stakeholders – public and private – and we’re trying to find a model where everybody is comfortable to contribute and will also be happy with the outcomes.”