Using a cocktail of fibre-reinforced epoxy-based thermosetting resins and 3D extrusion printing techniques, materials scientists at the Harvard School of Engineering and Applied Sciences (SEAS) and the Wyss Institute for Biologically Inspired Engineering have managed to develop cellular composite materials of unprecedented light weight and stiffness.
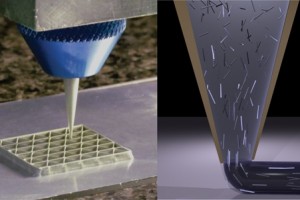
According to the press release by Harvard University, the materials can potentially be used as a replacement for the light-weight and stiff balsa wood because of their mechanical properties and the fine-scale control of fabrication.
The fast-growing balsa wood is renowned and valued for its light weight and stiffness relative to density, but is really expensive and natural variations in the grain can be an impediment to achieving precise performance requirements in sophisticated applications in various industries.
The work could have applications in many fields, for wind turbine, automotive and aerospace applications, where high stiffness- and strength-to-weight ratios are needed.
“By moving into new classes of materials like epoxies, we open up new avenues for using 3D printing to construct lightweight architectures. Essentially, we are broadening the materials palette for 3D printing. Balsa wood has a cellular architecture that minimises its weight since most of the space is empty and only the cell walls carry the load. It therefore has a high specific stiffness and strength. We’ve borrowed this design concept and mimicked it in an engineered composite,” says principal investigator Jennifer A. Lewis, the Hansjörg Wyss Professor of Biologically Inspired Engineering at Harvard SEAS.
A paper describing their results has been published online in the journal Advanced Materials.
“This paper demonstrates, for the first time, 3D printing of honeycombs with fibre-reinforced cell walls. Of particular significance is the way that the fibres can be aligned, through control of the fibre aspect ratio — the length relative to the diameter — and the nozzle diameter. This marks an important step forward in designing engineering materials that mimic wood, long known for its remarkable mechanical properties for its weight,” said Lorna Gibson, a professor of materials science and mechanical engineering at the Massachusetts Institute of Technology and one of world’s leading experts in cellular composites, who was not involved in this research.
The new composite material is considered a potential revolutionary invention since it mimics and even improves on balsa and the best commercial 3D printed polymers and polymer composites currently available.
“As we gain additional levels of control in filler alignment and learn how to better integrate that orientation into component design, we can further optimise component design and improve materials efficiency,” adds Brett G. Compton, a staff scientist in additive manufacturing at Oak Ridge National Laboratory.
“Eventually, we will be able to use 3D printing technology to change the degree of fibre filler alignment and local composition on the fly.”