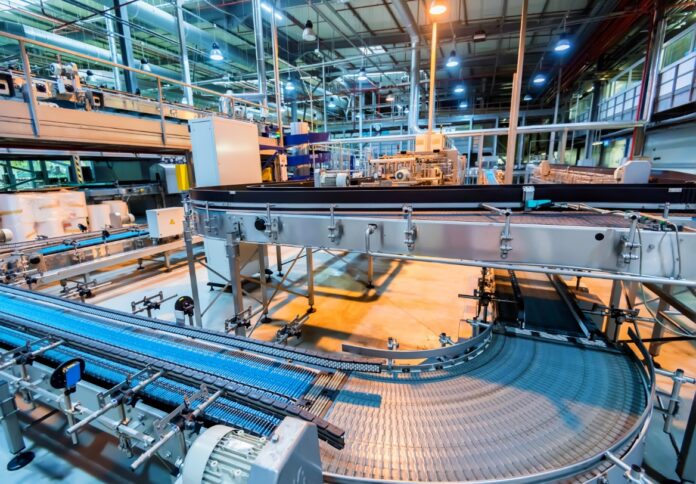
Article by Andrew Mamonitis, ECI Solutions' Vice President – APAC, Manufacturing Division,
In the current state of manufacturing, rising labour costs, energy process, and ongoing supply chain issues have identified the need for sharper cost control.
In this environment, understanding Total Manufacturing Costs (TMC) – the true cost of producing goods – has become essential not only for profitability, but for survival.
Total Manufacturing Cost (TMC) represents the comprehensive sum of all expenses incurred during the production process, and it is a vital metric for small-to-medium-sized business (SMB) manufacturers striving to remain competitive.
Understanding TMC
TMC encompasses every expense from raw materials, labour, machine depreciation, and overhead costs – factors that cumulatively influence the bottom line. For SMB manufacturers operating under tight budgets and competitive conditions, having a clear grasp of these costs provides essential insight into financial requirements and operational efficiency.
This understanding is the bedrock on which sound pricing strategies and profitability assessments are built. In today’s complex economic environment, any misstep in cost estimation can have far-reaching consequences, potentially jeopardising the company’s sustainability in a crowded marketplace.
The business case for accurate cost calculation
Inaccurate cost calculations pose significant risks. Without a structured process to determine TMC, businesses may unknowingly underprice products, inadvertently sacrificing profit margins, or overprice and subsequently lose market share.
The precise calculation of manufacturing costs allows SMBs to pinpoint inefficiencies and identify opportunities for cost savings. When manufacturers meticulously track and analyse TMC, they become equipped to make strategic decisions that impact pricing, production levels, and investment in innovation.
Accurate TMC is not just about understanding current expenses – It also plays a pivotal role in predicting future trends. As companies scale or modify their production processes, having an established baseline of manufacturing costs helps inform decisions on resource allocation, supply chain management, and technological upgrades.
This is particularly true in Australia and New Zealand where distance to global suppliers and higher operational costs leave little margin for error.
This foresight is invaluable, particularly when navigating unpredictable market forces and competitive pressures.
Optimising pricing strategies using TMC
At the heart of effective business management lies the ability to set competitive yet profitable product prices. With a clear picture of TMC, manufacturers can confidently determine a floor price that covers all incurred expenses while providing a reasonable profit margin. This precision in pricing ensures that products are not only appealing to consumers but are also sustainable from a cost perspective.
An accurate assessment of manufacturing costs empowers SMB manufacturers to fine-tune their pricing strategies. Detailed cost breakdowns allow businesses to explore various pricing models, adjust markups based on market conditions, and even introduce tiered pricing strategies that cater to different customer segments.
In an economy where every cent counts, a strategic pricing approach backed by solid TMC figures is often the linchpin between a thriving business and one that struggles to remain afloat.
Strategic financial planning and TMC
Beyond operational improvements, TMC serves as a foundational tool for comprehensive financial planning. Investment decisions, whether in new equipment, technology upgrades, or expanding the workforce, are greatly influenced by a company’s current cost structure.
For many manufacturers, accurately knowing the TMC facilitates informed decision-making about scaling production or entering new markets. Additionally, with wage pressures from skills shortages impacting trades like metal fabrication and CNC machining across Australia and New Zealand, accurate cost data is key to future-proofing the business.
Financial forecasting, when coupled with a solid understanding of TMC, also allows manufacturers to simulate different growth scenarios. Companies can evaluate the potential financial impact of various strategic moves, from increasing production capacity to introducing new product lines.
This proactive stance not only hedges against unforeseen market disruptions but also positions the company to seize opportunities as they arise.
TMC as a competitive differentiator
In an increasingly saturated marketplace, the ability to manage and optimise manufacturing costs can be a key competitive differentiator. SMBs that actively harness detailed TMC analysis are better positioned to offer competitive pricing without sacrificing quality.
Moreover, such companies are often more agile, responding to market shifts and technological advancements more effectively than competitors with less rigorous cost management practices.
Companies that excel in this area often set industry benchmarks, influencing not only their internal operations but also the broader manufacturing landscape.
The future of manufacturing cost management
The manufacturing sector continues to evolve with rapid technological advancements and shifting economic paradigms. In this context, the role of TMC is poised to become even more integral.
Automation, artificial intelligence, and predictive analytics are transforming how costs are calculated and managed. Manufacturers who invest in modern analytical tools can more accurately predict variable costs and adapt their processes accordingly.
As global supply chains face increasing volatility, a detailed understanding of TMC can help companies navigate disruptions with greater resilience. Cost transparency not only enhances internal decision-making but also builds trust with investors and partners by demonstrating a commitment to financial discipline and operational efficiency. Additionally, with sustainability reporting gaining momentum in Australia and New Zealand, cost transparency is becoming a key differentiator in the market.
For SMB manufacturers, the imperative to decode and master total manufacturing cost is clear. By establishing robust cost tracking and analysis systems, companies can unlock the potential for enhanced pricing strategies, improved operational efficiencies, and solid financial planning.
In today’s competitive manufacturing environment, those that leverage detailed TMC insights will likely lead the way in innovation and profitability, setting new standards for industry success.
For SMB manufacturers in Australia and New Zealand, mastering Total Manufacturing Cost isn’t just good business — it’s a necessary defence against the region’s unique cost challenges and a springboard to long-term growth.