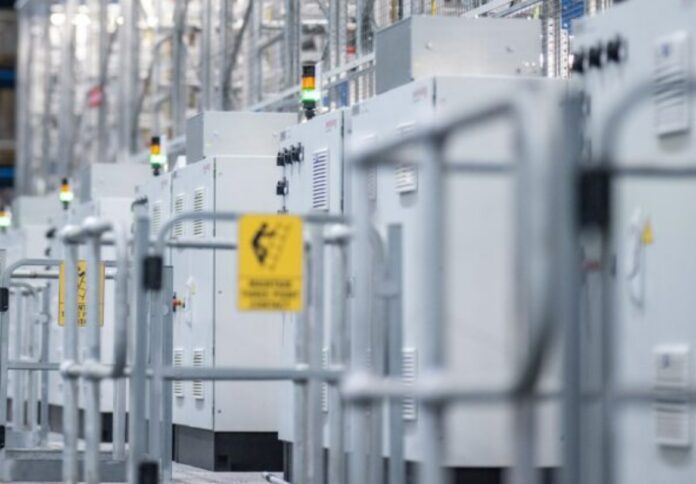
Article by Dan Ulmamei, Managing Director, Swisslog Australia and New Zealand
As we enter 2025, warehouse automation and intralogistics continue to be shaped by technological innovation, evolving consumer demands, labour challenges and space scarcity, and a continued drive to optimise performance and efficiency.
Organisations are increasing investments in proven automation technologies and unlocking new efficiencies through software orchestration and artificial intelligence. These advancements are transforming the intralogistics landscape and setting the stage for industry changes. Let’s explore four key trends expected to shape the industry in 2025.
- Brownfield Warehouse Automation and the Importance of Scalability
With industrial land prices continuing to rise in Australia and New Zealand, particularly in and around major cities, it is becoming increasingly important for companies to make the most of their existing space with retrofits, modernisations, or upgrades to new technologies that bring greater efficiencies.
There are numerous reasons for modernising or upgrading a warehouse automation system, typically centred around optimising current operations and investing in enhancements that are cost-effective and deliver long-term benefits.
Upgrading to the latest warehouse technology or software can deliver immediate benefits to energy efficiency, safety, data acquisition and utilisation, and maintenance schedules, particularly for equipment nearing end of design life, which may be harder to maintain.
Scalability is crucial when considering any automation investment, because if business expands, you want your warehouse to be able to handle additional or different SKUs, and greater volumes – and the quicker it can adapt, the quicker the business can reap the benefits of its growth.
- Micro-Fulfillment and Hub-and-Spoke Strategies
Micro-fulfillment centres (MFCs) are the next step in creating a harmonious omni-channel supply chain, and have been growing in popularity particularly in the past five years, with the trend continuing in 2025.
A MFC model is a form of hub-and-spoke strategy whereby a centralised fulfillment centre (the hub) stores a large amount of stock, and then each spoke holds some stock, that is replenished efficiently from the hub. The spokes are often stores themselves, but can also be straight to home delivery centres, for example.
Hub-and-spoke models are particularly popular with top grocery companies, where freshness and efficient deliveries are paramount.
Automated MFCs allow companies with or without a brick-and-mortar footprint within a particular area to move fulfillment closer to customers in order to reduce transportation costs and enable shorter delivery times, benefitting both the retailer and the customer. Companies can build a micro-fulfillment centre as a standalone facility, or bolted on to an existing location, to expand fulfillment capacity.
The mutual benefits of MFCs are likely to drive their continued expansion this year, as supply chains look to further increase their efficiency and profitability. For consumers, it is all about increased choice, shorter delivery times or the ability to order online and arrange curb-side pickup as quickly as possible. For grocers and retailers, it is a more efficient method of order fulfillment. It reduces labour and transport costs, avoids clogging retail stores with pickers and supports higher order demand levels. In other words, MFCs create a more efficient supply chain.
- Software Orchestration
For warehouse automation and intralogistics systems to perform at their peak, and deliver maximum return, the right software can make a big difference.
For both greenfield and brownfield warehouse automation projects, companies looking to take operations to the next level in 2025 will use software orchestration to optimise performance.
Swisslog’s SynQ Warehouse Management System (WMS), for example, covers the full spectrum of an organisation’s supply chain needs to optimise warehouse operation in the era of Industry 4.0. It is the smart conductor of the orchestra that synchronises people, process, and machines for efficient operations.
SynQ software performs not only WMS tasks, but also Material Flow System (MFS) and Warehouse Control System (WCS) functions as well. To take it to the next level, SynQ also has proven interfaces for other systems including Enterprise Resource Planning (ERP), and can be customised to interact with companies’ proprietary systems too.
SynQ modules can include real-time monitoring and full 3D visualisations of the warehouse, with “click-and-solve” functionality. This means, for example, that an operator can access any pallet within the automated warehouse, and can make changes to that pallet directly – such as sending it to the reject station, or to a clearing station to be checked if something doesn’t look right.
- Artificial Intelligence and Robotics
Just about every industry is talking about artificial intelligence (AI) and robotics, but there are some tangible benefits in the intralogistics industry, which has been using these tools for years already, and they are only getting smarter and more capable.
AI-powered systems can enable accurate demand forecasting, predictive maintenance, real-time inventory management, and seamless integration with warehouse automation solutions. These insights streamline order fulfillment, optimise material flow, and boost overall supply chain performance, enabling warehouses to meet increasing demands with precision.
Sophisticated WMS and data analytics tools will provide real-time insights on inventory levels, order patterns, and operational bottlenecks. By leveraging machine learning, AI, and advanced algorithms, these data-driven solutions can identify patterns, accurately predict demand, optimise resource allocation, and streamline processes for maximum efficiency.
Moreover, predictive maintenance capabilities enabled by data analytics will minimise equipment downtime, further enhancing operational efficiency and reducing costly disruptions.
To complement AI and software, robots are taking on tasks such as picking, packing and maintenance, highlighting the growing inclination among forward-thinking companies to leverage automation for process optimisation and efficiency improvements.
In 2025, advancements in Automated Storage and Retrieval Systems (ASRS), and Autonomous Mobile Robots (AMRs) will continue transform dynamic warehouse operations.
ASRS technologies will also help companies maximise their floor space, which is particularly helpful in driving ROI for sectors like grocery and retail.
Conclusion
Swisslog is seeing these trends not just across Australia and New Zealand, but globally too. Swisslog can draw upon its extensive local and global knowledge to design and implement solutions in our region that are fit-for-purpose and designed to deliver optimum returns.
As we continue to deliver optimised solutions in 2025, Swisslog will be focusing on key areas, including:
- The human side of automation, and seeing where robotics, automation, and software can make people’s jobs easier and more efficient – or where they can deliver greater benefits to people. This company-wide strategy emphasises Swisslog’s commitment to placing people at the forefront of our mission. Through expertise and collaboration, Swisslog colleagues become an extension of our customers’ teams, sharing their aspirations, challenges, and successes.
- Lifetime customer support, beyond project implementation. A warehouse automation solution is an important long-term investment, and one that can be continually optimised, maintained, and adapted as a business grows and changes. Swisslog’s model is to support our customers for the entire lifetime, in a true partnership, not to just sell the technology and move on.
- Sustainability, which is a key focus for most Australian and New Zealand companies, as they seek to meet key Environmental and Social Governance (ESG) goals, reduce their footprint, and minimise their impacts on the environment. Both Australian and New Zealand governments have goals to reach Net Zero emissions by 2050, and industries like intralogistics can play a part in this transition. Electric automation technologies, like robotics, are energy-efficient, using as little as 0.1 kW per hour, and can be powered by renewable sources.
With these strategic approaches in mind, Swisslog will enable Australian and New Zealand companies to embrace trends like brownfield automation, MFCs, software, AI, and robotics, to futureproof operations and gain a competitive edge. Intralogistics is evolving rapidly, and companies that adapt to these trends will thrive in an era of futuristic, highly optimised warehouses.