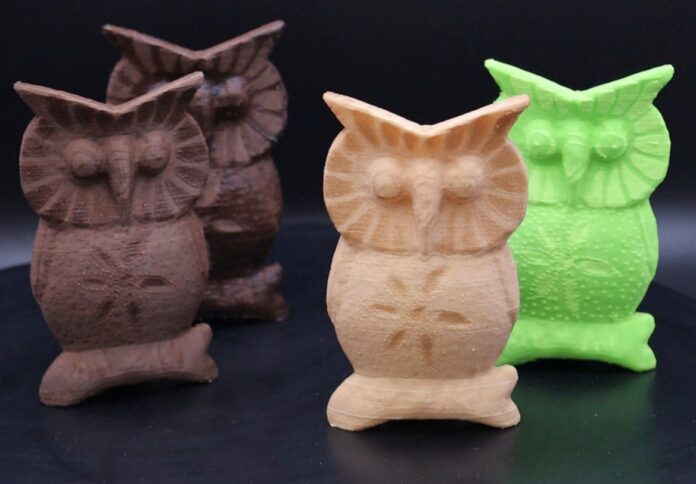
Researchers from the Massachusetts Institute of Technology (MIT) and Delft University of Technology have unveiled a new 3D printing technique that improves the efficiency of producing customised objects while minimising material waste.
This method, known as speed-modulated ironing, utilises heat-responsive materials to create intricate, multi-textured items in a single printing process, eliminating the need for time-intensive nozzle changes, MIT revealed in a news release.
According to researchers, conventional multimaterial 3D printing methods often require the use of multiple nozzles, which leads to excessive material waste and longer production times.
In contrast, the newly developed technique employs a dual-nozzle printer.
The first nozzle deposits a heat-sensitive filament, while the second nozzle, functioning as an “ironing” tool, applies heat to manipulate the material’s properties, including color and texture.
By adjusting the speed of the second nozzle, researchers can achieve specific levels of opacity and texture without requiring any modifications to the printer’s hardware.
Mustafa Doga Dogan, a PhD candidate at MIT and co-author of the research, emphasised the technique’s potential: “Today, we have desktop printers that use a smart combination of a few inks to generate a range of shades and textures. We want to be able to do the same thing with a 3D printer — use a limited set of materials to create a much more diverse set of characteristics for 3D-printed objects,”
This research, a collaboration between Dogan, Zjenja Doubrovski at TU Delft, and Stefanie Mueller from MIT’s Electrical Engineering and Computer Science Department and CSAIL, will be showcased at the upcoming ACM Symposium on User Interface Software and Technology.
Harnessing speed to control heat
According to researchers, the motivation behind this research was to explore more effective ways to achieve multiproperty 3D printing using a single material.
Traditional methods typically rely on a single nozzle for both printing and heating, which can be time-consuming and can degrade the filament.
To overcome these challenges, the team developed a technique that prints with one nozzle and uses a second nozzle to reheat the material.
Marwa AlAlawi, a graduate student in mechanical engineering at MIT, compared the process to moving a finger over a flame, explaining that the speed at which the second nozzle moves affects the temperature of the material being heated.
This allows for varying temperatures to be achieved without altering the heating source.
The researchers created a theoretical model to determine the required speed for the second nozzle to heat the filament to precise temperatures that correspond to specific colours and textures.
They integrated this model into a user-friendly interface, converting the pixels in a 3D model into detailed printing instructions.
Efficiency and versatility in production
In their experiments, the team tested three different heat-responsive filaments.
The first, a foaming polymer, was capable of producing various shades and textures by expanding when heated.
The researchers also experimented with filaments containing wood and cork fibres, which could be charred to create darker colours.
Demonstrations of the new technique included the production of partially translucent water bottles and textured bike handles designed to enhance grip.
The speed-modulated ironing method drastically reduced printing time compared to traditional multimaterial approaches, which can often prolong production by hours and increase material consumption.
Looking forward, the research team plans to explore additional thermally responsive materials and investigate how speed-modulated ironing can modify the mechanical and acoustic properties of certain objects.