Additive manufacturing has been around for quite some time; individuals and businesses alike have been all over the technology, trying to come up with new ways of implementing it. Many say that additive manufacturing is the future of manufacturing, and 3D Systems has made one giant step toward that future, delivering a major breakthrough in the field.
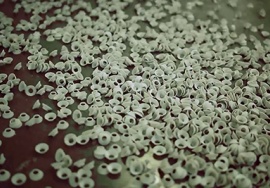
In a media release, 3D Systems announced that their fab-grade 3D printers have matched and exceeded the productivity and speed of traditional moulding, in creating functional parts. In layman’s terms, the company has opened the gate towards the development of extremely productive machines with high speeds and capable of producing both indistinguishable and customised parts with their precision Stereolithography (SLA®) and Selective Laser Sintering (SLS®) advanced manufacturing printers.
“Our unwavering commitment to customer success through innovation has literally broken the mould this time — challenging the myth that 3D printing can’t match the productivity of injection moulding,” said Cathy Lewis, Chief Marketing Officer at 3D Systems Corporation.
“This is just the beginning. We are working on additional applications that defy traditional manufacturing constraints, allowing our customers to go from idea to product in hours, instead of months — to truly manufacture the future.”
The company claims that 3D printers have managed to double their capabilities every 18 months. As an example, 3D Systems points out the 2400 printed lamp shades in 20 hours with one of their stereolithographic printers; in other words, it took them about 30 seconds to print out one lamp shade. Remember that the process does not require any tools or lengthy supply chains.
We can safely say that 3D printing is much more effective than traditional injection moulding techniques.
3D Systems is débuting a series of videos that show their fab-grade printers in action.
To learn more, please visit www.3dsystems.com