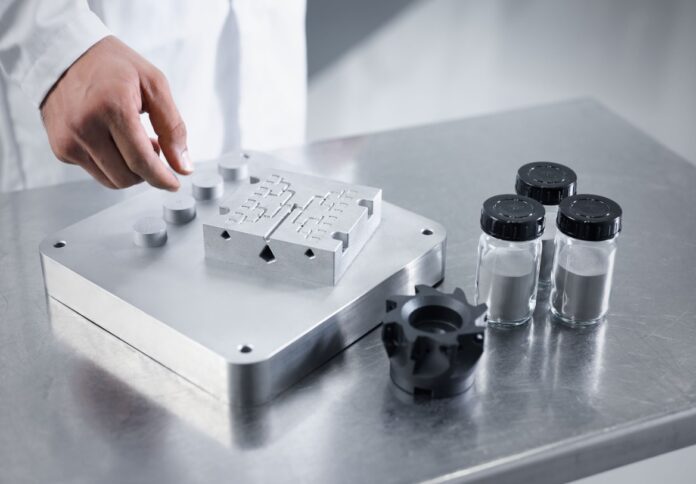
Sandvik, a global leader in metal powder technologies, announced the launch of Osprey HWTS 50, an advanced hot-work tool steel powder designed for laser-based Additive Manufacturing (AM).
This new product is optimised to improve printability and processability, making it highly suitable for a range of applications, including Laser Powder Bed Fusion (L-PBF), Hot Isostatic Pressing (HIP), and Metal Injection Molding (MIM).
According to Sandvik, Osprey HWTS 50 addresses common challenges in hot-work applications within general engineering, including reducing the risk of cold cracking during Laser Powder Bed Fusion (L-PBF) processes.
The steel is intended for use in high-pressure die casting, injection moulds, and hot forming tools, and its chemical composition is optimised for improved hot hardness at temperatures exceeding 600°C (1,112°F).
The product features a lower carbon content than medium-carbon hot-work tool steels, with adjustments to carbide-forming elements to enhance tempering resistance.
Sandvik states that Osprey HWTS 50’s high thermal conductivity ensures efficient heat dissipation, which is advantageous for applications such as die casting and forging, where rapid heat removal can speed up production cycles.
Faraz Deirmina, Principal Metallurgist at Sandvik, emphasised the product’s benefits for AM tooling, noting that Osprey HWTS 50 was developed to address fabrication challenges in tools and dies produced using additive manufacturing technologies.
The powder is manufactured using either Vacuum Inert Gas Atomization (VIGA) or Inert Gas Atomization (IGA), resulting in spherical particles that offer good flow characteristics and high packing density.
Additionally, the powder has low oxygen content and impurity levels, contributing to improved mechanical performance.
Key features of Osprey HWTS 50 include enhanced processability in L-PBF, optimised chemical composition for hot hardness and tempering resistance, and high thermal conductivity.
The material’s hardness ranges from 40 to 50 HRC, depending on tempering temperature, ensuring durability in high-stress conditions.
Applications for Osprey HWTS 50 include mould making, extrusion dies, hot forging, die casting tooling, plastic moulding, and tool repair.
The steel is also suited for rebuilding die-casting molds through Direct Energy Deposition (DED).
Sandvik has filed a patent for the composition of Osprey HWTS 50 and highlights that the alloy design reflects the company’s commitment to resource efficiency and sustainability, as the lean composition helps reduce energy consumption and carbon emissions.
For further details, visit Sandvik’s website.