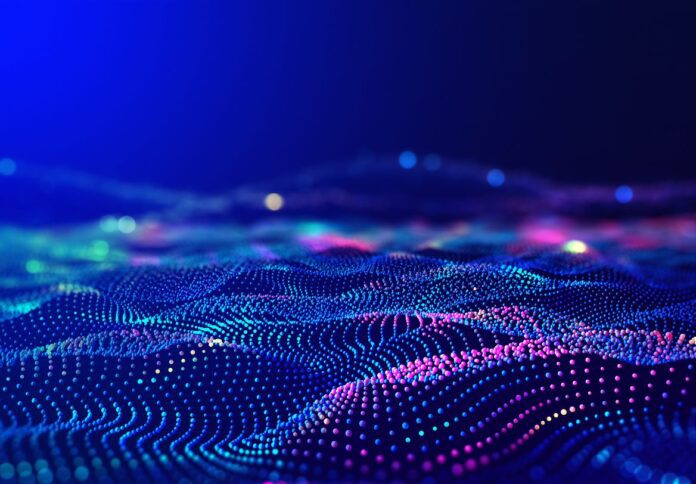
Article by James Robinson, Head of Services for Asia Pacific at SYSPRO
The Australian Industrial Manufacturing, Fabricated Metals and Engineering sectors make a significant contribution to our economy, playing a vital role in industrial development, aiding economic growth and employment.
According to data from the Australian Government’s Jobs and Skills Australia (JSA) department, manufacturing overall employs approximately 6.3 per cent of the Australian workforce.
Encouragingly, the manufacturing sector has shown resilience and growth over the past year, adding 14,800 new workers, a 1.7 per cent increase as of May 2024. Similarly, the Australian Bureau of Statistics (ABS) reported a 1.9 per cent increase in manufacturing turnover in the year leading to June 2024.
These statistics highlight the sector’s potential, but they also reveal a pressing issue: skilled labour shortages remain a significant challenge that must be urgently addressed with strategic solutions to sustain the current growth trajectory.
The impact of labour shortages on the Industrial Manufacturing sector
Despite recent positive employment numbers, the Industrial Manufacturing sector struggles with a lack of skilled talent. JSA data shows that median weekly earnings in manufacturing are $1,512, falling short of the all-industry median of $1,600. This wage disparity means the Industrial Manufacturing sector must reconsider its compensation strategies to attract and retain talent, especially in a competitive labour market where skilled workers have options across other industries.
However, attracting talent by increasing wages creates a catch-22 for Industrial Manufacturing companies. Raising salaries can lead to higher overheads, reduced profit margins and increased product prices, which could drive inflation. This presents a delicate balance for manufacturers, especially those in Australia’s Industrial Manufacturing sector, which already faces high operational and wage costs compared to global competitors.
According to our Global CFO Manufacturing Survey, 86 per cent of Australasian respondents reported that labour shortages are the most significant bottleneck causing instability in their business. The lack of skilled workers adds pressure to day-to-day operations, disrupting supply chains. Over half of respondents noted that securing skilled talent is a significant barrier to maintaining smooth supply chain operations.
How ERP systems help mitigate labour shortages
Enterprise resource planning (ERP) systems have emerged as a powerful solution for IME manufacturers grappling with skilled labour shortages. While finding qualified workers is becoming increasingly tricky, manufacturers can turn to technology to optimise their existing workforce, enhance efficiency and ultimately mitigate the impact of labour shortfalls.
An ERP system provides Industrial Manufacturers with a unified platform that integrates various business functions such as finance, procurement, production, inventory management, and human resources. This interconnectedness is critical for streamlining processes, reducing redundancy, and increasing departmental transparency.
When implemented effectively by a manufacturing specialist, ERP systems can significantly reduce manual work, enabling industrial manufacturing companies to maintain high productivity levels despite having fewer workers. Here are three key ways ERP system can help an industrial manufacturing company.
Workforce optimisation and efficiency
ERP systems offer powerful analytics to help industrial manufacturing companies optimise their existing labour force. These systems enable manufacturers to forecast labour needs, track employee productivity and identify inefficiencies.
With real-time data, industrial manufacturing companies can make informed decisions about staffing levels, allocate resources more effectively and even implement cross-training programs to upskill existing employees.
Optimising the workforce becomes essential in an environment where skilled workers are scarce. ERP systems can help identify bottlenecks and offer solutions, such as reallocating workers to high-priority areas or adjusting production schedules to align with available resources. This level of agility is crucial for industrial manufacturing producers trying to maintain productivity during labour shortages.
Enhancing decision-making through data-driven insights
One of ERP systems’ greatest strengths is their ability to provide data-driven insights. By consolidating information from different departments into a centralised platform, ERP systems allow managers to gain a holistic view of the business. This real-time visibility can be precious when dealing with labour shortages.
For instance, if a manufacturer is experiencing production delays due to a lack of skilled workers, ERP data can quickly identify the root cause of the problem, whether it’s an issue with scheduling, training, or resource allocation. Managers can then adjust their strategies accordingly, using ERP insights to make data-driven decisions that mitigate the impact of worker shortages.
Supply chain resilience
Labour shortages affect production and can have a ripple effect on the entire supply chain. With fewer workers available to manage logistics, inventory control and procurement, the risk of supply chain disruptions increases. ERP systems can help industrial manufacturing, fabricated metals and engineering companies build more resilient supply chains by providing end-to-end visibility and automating critical processes like order tracking, supplier management and demand forecasting.
By leveraging ERP systems, Industrial manufacturers can anticipate disruptions in the supply chain and adjust their production plans accordingly. For example, if a worker shortage delays the production of a critical component, the ERP system can reroute resources to ensure other areas of the production line remain operational. This level of flexibility is crucial for maintaining supply chain continuity, especially in an environment where labour shortages are unpredictable.
Conclusion
The Australian IME sector is at a pivotal moment. With demand for their goods on the rise and technological advancements pushing the industry forward, IME producers have a unique opportunity to thrive. However, labour shortages remain a critical challenge threatening the sector’s ability to scale and compete globally.
ERP systems are vital solutions in navigating this complex challenge. By automating processes, optimising workforce utilisation and enhancing supply chain resilience, ERP systems enable Australian IME manufacturers to do more with less. For those who fully leverage a manufacturing ERP system, it could represent the difference between stagnation and sustained growth in the global economy.