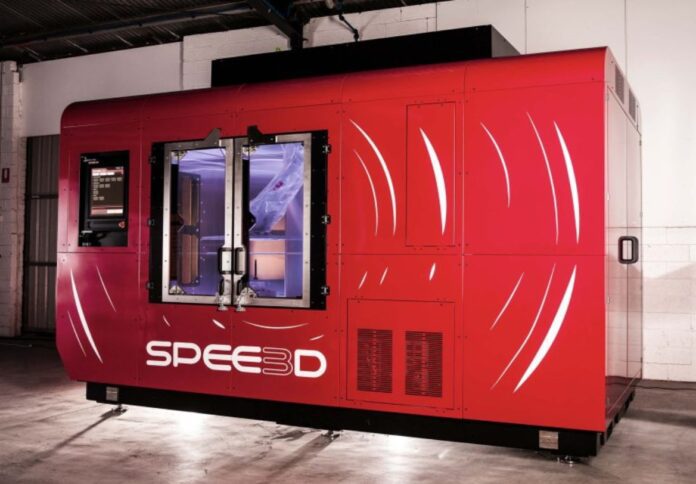
Victoria-based additive manufacturing company SPEE3D has showcased its advanced technology in a high-stakes demonstration hosted by the US Army Combat Capabilities Development Command (DEVCOM) Army Research Laboratory (ARL) at the University of Tennessee Knoxville.
The demonstration, which ran from 5 to 16 August 2024, aimed to train a soldier with no prior additive manufacturing experience to produce a critical metal part using SPEE3D’s innovative cold spray additive manufacturing (CSAM) technology.
The soldier, unfamiliar with SPEE3D’s CSAM technology, was tasked with printing a transmission mount for a Bradley Fighting Vehicle, the company said in a news release.
The part was subsequently installed in a vehicle, which underwent rigorous testing in the 278th field test area. After several test cycles, the component showed no signs of degradation.
This trial highlighted the capability of SPEE3D’s technology to deliver essential repair parts and restore operational functionality in the field.
“SPEE3D intends to make additive manufacturing accessible as a quick, cost-effective, and easy way to print crucial metal parts that otherwise would not be available at the point of need,” said Byron Kennedy, CEO of SPEE3D.
He continued, “Having a soldier with no previous additive manufacturing experience learn our technology within a week certainly meets that goal. We are proud to have collaborated with Army Research Labs, the University of Knoxville, the 278th Armored Cavalry Regiment, and all of our other partners to participate in this successful demonstration.”
The exercise was organised by DEVCOM ARL, with the University of Tennessee Knoxville serving as the demonstration host, and the 278th Armored Cavalry Regiment (ACR) providing site support.
VRC Metal Systems also participated in the demonstration. The final presentation of the printed part took place on August 15 at the ACR Armory in Livingston, Tennessee, with notable figures in attendance.
“This demonstration successfully illustrated how cold spray technology can be utilized to positively impact the warfighter in expeditionary scenarios,” commented Michael Nicholas, Materials Engineer at DEVCOM ARL.
He continued, “Expeditionary cold systems provide added repair and manufacturing capabilities, addressing supply chain challenges typical in contested logistics environments. Overall, this advanced manufacturing demonstration was extremely successful due to our amazing partnerships with industry, academia, and future technology users.”