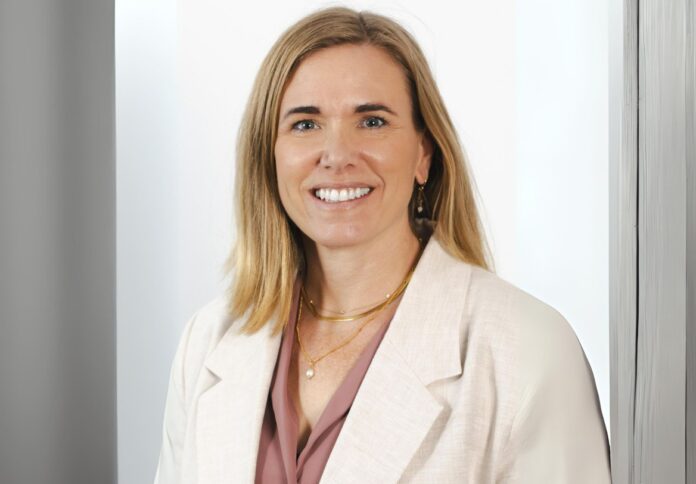
As the world pivots towards sustainability, Australia’s manufacturing sector faces significant challenges in ensuring long-term water security.
Kristi McLachlan, regional director, Water Australia Asia at Hatch, a global engineering and project delivery firm, has shared her insights on the critical role of water management in driving the success and sustainability of manufacturing in Australia.
Lack of holistic water security perspective
Australia’s manufacturing sector is grappling with a fundamental challenge: the nation lacks a whole-of-society perspective on water security, not just for drinking but also for industrial and commercial needs.
McLachlan emphasised that this is a pressing issue that needs to be addressed immediately and into the future. “With the focus on a Future Made in Australia driving the renewables transition and the move to ‘net zero,’ water is a fundamental piece of the puzzle in the production of hydrogen and in the supply chain for transmission, generation, and storage,” she said.
One of the most concerning aspects, according to McLachlan, is the tendency to use water for one activity, only to create a cascade of other issues. “Our modus operandi is to shift risks rather than solve problems,” she explained.
For instance, the sector often overlooks the potential of wastewater, which is typically discharged into the environment or stored in large dams.
McLachlan urged a rethink: “Wastewater is still a resource – it doesn’t necessarily have an ‘end of useful life.’ Other manufacturing industry players or even operators in other industries may have a use for it.”
The critical role of water in manufacturing sustainability
The urgency of prioritising water management cannot be overstated. As Australia drives towards an energy transition, the demand for water is increasing, particularly in the production of green hydrogen. “We’ve seen projects stopped due to the lack of consideration of water sources,” McLachlan noted.
The push for rain-independent water sources, such as desalination plants, is growing, but these solutions are capital and power-intensive.
Moreover, McLachlan highlighted the growing importance of supply chain transparency from a social licensing perspective.
“Water consumption and management is becoming increasingly a part of that consideration,” she said, adding that water authorities are tightening regulations on contaminants and organic matter in trade waste discharge, significantly driving up operating costs.
Quantifying water requirements in manufacturing
Water requirements vary across different manufacturing processes, influenced by factors such as climate, geography, and technology. McLachlan provided detailed insights into the water usage associated with various industries:
- Clothing production: The textile industry is notoriously water-intensive, with approximately 2,700 litres of water needed to produce a single cotton T-shirt. Manufacturing a pair of jeans takes about 8,183 litres of water.
- Food manufacturing: The water footprint of food production is equally staggering. For instance, it takes about 628 litres of water to produce a single litre of cow’s milk, compared to 371 litres for almond milk and 28 litres for soy milk. Grain crops also demand significant water, with 5,000 litres required for 1kg of rice.
- Hydrogen production: Hydrogen production requires a substantial amount of water, with 9-11 litres needed to produce 1kg of green hydrogen through electrolysis. Cooling water requirements can further increase the water demand, making hydrogen production a highly water-intensive process.
- Mining extraction: Mining operations are also heavy water users, with 500,000 litres required to extract and process a tonne of copper. Gold extraction demands about 1,060 litres of water per gram of gold.
Steps to reduce water and consumption waste
Manufacturers must collaborate and innovate to reduce water consumption and waste. McLachlan suggested critiquing conventional practices and embracing new technologies.
“Examples exist where we are looking at dry processing in mining, operating chemical processes at higher concentrations, and designing for zero discharge facilities,” she explained.
Moreover, the need for industrial processes that use less water should be at the forefront of manufacturers’ thinking. McLachlan advised that manufacturers explore shared practices and resources within their regions and industries to drive efficiencies and contribute to a circular economy.
Managing water requirements for hydrogen production
As the manufacturing sector pivots towards hydrogen as a clean energy source, managing the significant water requirements becomes critical. McLachlan advocates for a broader systems view of water resources, emphasising the potential of repurposing wastewater for hydrogen production.
“When considering the water required for hydrogen production, a lot of the process water must be high purity. The current sources of high-purity water are almost fully allocated, which means conflicts and potential social license questions,” she warned.
Desalination plants, while providing climate-independent water sources, come with high costs in both capital and energy. Therefore, manufacturers must carefully evaluate the best use cases for these plants to ensure resilience without compromising sustainability.
The future of water security in Australia’s manufacturing industry
Looking ahead, McLachlan sees the intersection of the circular economy and Industry 4.0 technologies as key to enhancing water security in Australia’s manufacturing sector. “We can go better than traditional and conventional water usage and reusage practices,” she asserted.
The rising costs of water sourcing and treatment are already driving a shift in how water is managed, presenting an opportunity for innovative approaches to contribute to a water circular economy.
McLachlan also highlighted Australia’s geographical advantages and technological capabilities as factors that can be leveraged to ensure long-term water security.
“Our manufacturing sector is small but tight and open to digital transformation and disruption,” she said, pointing to the potential of machine learning and remote sensing in optimising water treatment processes.