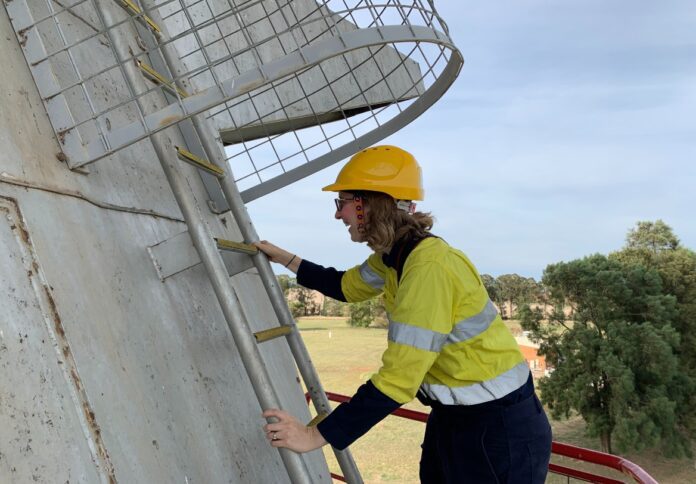
In the dynamic world of Hunter manufacturing, a new generation of innovators is stepping up to secure the industry’s future. Among these innovators is Jess Hodge, who, along with her husband Geoff, is transforming plastic waste into sustainable products through their company, Resourceful Living.
The company, based in Kurri Kurri, takes discarded plastic and turns it into practical items like furniture, clocks, and skirting boards. “From pollution to practical,” as they say, this process can take as little as two days.
Hodge remarked, “I’m young, Geoff is young, and we’re still a young business.” They started in a 100-square-meter premises in Beresfield three years ago and recently moved into a 2600-square-metre factory.
The company is in the first stage of expansion, adding new processing machines and conveyor belts to increase capacity from 50 tonnes of plastic waste a year to nearly 1000 tonnes.
Hodge shared, “We’re changing the business into a real circular operation.” This expansion is driven by demand, with their smaller machines at capacity, creating a month to six-week turnaround. A new crusher will manage larger waste items, allowing for the processing of 250 tonnes a month.
Resourceful Living plans to grow from four full-time employees to 25 in the next two years, hiring monthly to keep pace with the new machinery. Hodge said they are committed to keeping the operation local: “I’m trying to keep it all local and we can all be proud of our backyard.”
One of their significant markets is big corporates in Australia and New Zealand, including a national store redo for Sportsgirl. They are also collaborating with concreting firms, providing plastic sheets that outperform traditional formply in wet weather.
Hodge credits the Hunter Manufacturing Awards (HMA) for networking opportunities and mentorship. “We won the HMA outstanding start-up in 2022, which was just incredible. And then last year we won for best partnership.” This partnership involves transforming waste from Hunter New England Health into various products.
Curtis Gibson, general manager of AE Gibson & Sons and last year’s HMA rising star co-winner, is also at the forefront of Hunter manufacturing.
His company has been designing and manufacturing special purpose machinery for over 100 years, and Curtis sees the future in automation, robotics, and machine learning AI.
“Technologies such as automation, robotics, and machine learning AI are providing solutions to many of the challenges facing Australian manufacturers,” he says.
As times have changed, automation and robotics have improved efficiency, productivity, and safety. Gibson noted, “If we can automate those tough tasks, it provides manufacturers an opportunity to redeploy staff onto higher value-add activities.”
A recent project involved using robots for handling and stacking heavy timber panels, freeing up workers for more valuable tasks. Modern industrial robots, or cobots, work alongside humans to enhance productivity and safety.
“The ‘cobots’ work collaboratively with humans to enable the workers to be more effective, productive, and safe,” Gibson explained.
Elecbrakes is another company making waves in Hunter manufacturing. Managed by Toby Shaward, it has grown significantly in the three years Toby has been there.
Elecbrakes developed a trailer-mounted brake controller that provides proportional braking through an app/remote/CarPlay, eliminating the need for additional wiring in the vehicle cab.
Shaward highlighted the company’s rapid growth: “When I started, we were in a warehouse with only two engineers. We are now in a bigger, modern manufacturing facility with about 40 people and five engineers.”
Elecbrakes is constantly reassessing its processes to improve and scale effectively. One of their significant challenges is the intensive manual process required to manufacture wiring looms, a problem they are addressing through redesign and automation.
Lilly Großstück, a structural/civil engineer at Advitech, represents the future of manufacturing with her commitment to sustainable and integrated design.
After moving to Australia in 2020 and facing the challenges of the pandemic, Lilly has quickly risen through the ranks at Advitech. She emphasised the importance of considering the entire lifecycle of a product, from design to maintenance, to create a network among all involved in the manufacturing process.
Lilly’s work involves constant communication with fabricators, builders, end-users, and maintenance teams to ensure the product is safe, functional, and sustainable. Her dedication earned her a nomination for the HMA Rising Star award, recognising her contributions to the company and the industry.
Curtis Gibson sums up the challenges and solutions facing Australian manufacturers: speed to market, production flexibility, labour availability, skills, supply chains, input costs, and opportunities to develop new products and markets.
The content of this article is based on information supplied by Hunter Manufacturing Awards.