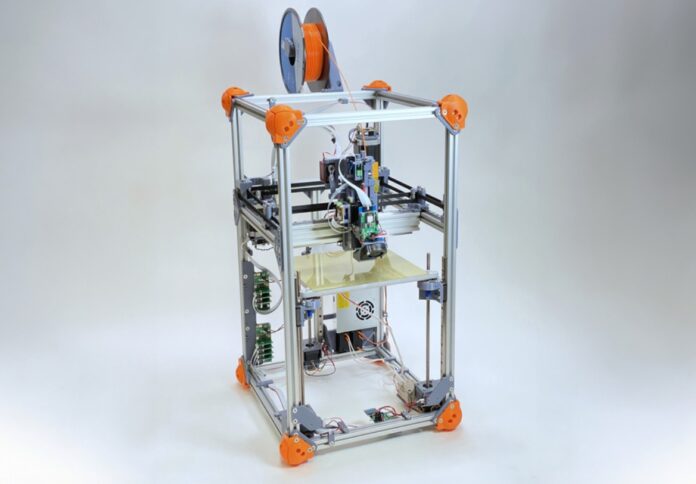
The 3D printing landscape is poised for a revolutionary shift with a groundbreaking innovation that aims to make the technology more sustainable and versatile.
A new 3D printer, developed through a collaboration between MIT’s Centre for Bits and Atoms (CBA), the US National Institute of Standards and Technology (NIST), and Greece’s National Center for Scientific Research (Demokritos), can autonomously determine the optimal printing parameters for previously untested materials.
In a news release, MIT said this advancement addresses a significant hurdle in the adoption of sustainable materials in 3D printing, potentially reducing the industry’s environmental impact.
Traditional 3D printing, or additive manufacturing, involves manual adjustments to accommodate new materials, particularly those that are recyclable or renewable.
Each material requires setting up to 100 parameters to ensure proper extrusion and object formation. This process, often perfected through tedious trial-and-error methods, has long been a barrier to using new, eco-friendly materials.
The innovative 3D printer developed by this international team incorporates modifications to its extruder, enabling it to measure critical forces and flows of any material fed into it.
These measurements are analysed through a mathematical function, which then generates the necessary printing parameters.
This automated process can replace about half of the manual adjustments typically required, as demonstrated in successful tests with various renewable materials.
“In this paper, we demonstrate a method that can take all these interesting materials that are bio-based and made from various sustainable sources and show that the printer can figure out by itself how to print those materials. The goal is to make 3D printing more sustainable,” explained Neil Gershenfeld, senior author and leader of CBA.
The modified extruder features a load cell to measure the pressure on the printing filament and a feed rate sensor to gauge filament thickness and feed rate.
These instruments collectively provide the data needed to determine two crucial yet elusive parameters: flow rate and temperature. These parameters are integral to setting up the slicer software that directs the printer.
The team’s breakthrough involved a 20-minute test that generates essential temperature and pressure readings at different flow rates.
This test, crucial for setting the extruder’s limits without causing damage, led to the “aha” moment that facilitated the accurate automatic parameter generation.
The researchers have validated their method through experiments with six different materials, including several bio-based ones, successfully producing complex objects with consistently viable parameters.
Their next steps include integrating this automatic parameter generation directly into 3D printing software, eliminating the need for manual input, and enhancing their workflow with a thermodynamic model of the printer’s hot end.
By enabling the use of recycled and bio-based filaments with variable properties, the new method significantly enhances the potential of digital manufacturing to utilise locally sourced sustainable materials.
This aligns with the broader goal of advancing computational metrology, where the outcome of measurements leads to predictive models, rather than just parameters, to further innovate advanced manufacturing.
“This fusion of measurement, modelling, and manufacturing is at the heart of the collaboration between NIST and CBA, as we work to develop what we’ve termed ‘computational metrology,’” added James Warren, who leads the Materials Genome Program at NIST.
As 3D printing continues to evolve, this research, supported by NIST and the Center for Bits and Atoms Consortia, represents a significant stride towards a more sustainable and adaptable manufacturing future.