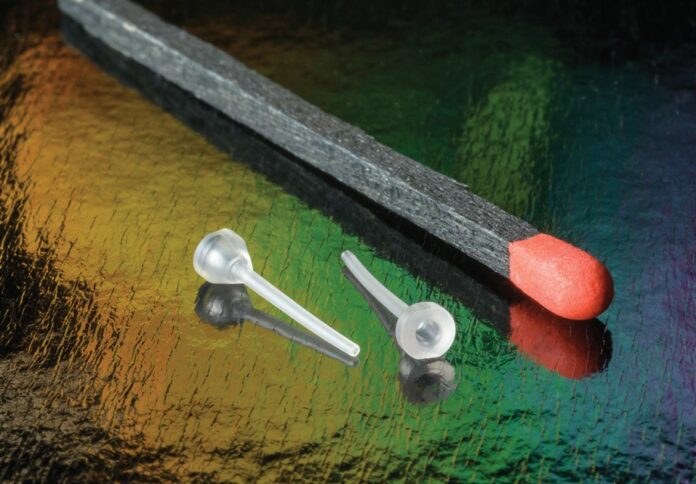
Article by Paul Runyan, VP Sales & Marketing, Accumold
In the dynamic medical field, micro moulding has increasingly become the foundation for innovation, particularly in the creation of cutting-edge biomedical devices.
This article explores the transformative impact of micro moulding within the biomedical industry, and highlights how the unparalleled precision, scalability, and customization offered by micro moulding are paving the way for future breakthroughs in patient care.
Furthermore, we examine how these technologies facilitate the miniaturization of devices, making procedures less invasive and more efficient, thereby significantly enhancing patient outcomes.
The insights presented underscore the critical role that micro moulding plays not only in current medical device development but also in shaping the future landscape of healthcare technologies.
Micro moulding
Micro molding is a specialized manufacturing technique that involves the production of extremely small components, crafted from broad palette of different polymers, and characterized by their high precision and meticulous accuracy. The significance of micro moulding is highlighted by its critical role in the development of miniature medical devices featuring intricate shapes and made from advanced, high-performance materials, which are increasingly required for innovative healthcare applications. These applications include, but are not limited to, tiny implants, sophisticated surgical tools, and advanced diagnostic equipment. This capability to fabricate small-scale, complex components is essential as it supports the advancement of medical technology and enhances the functionality and effectiveness of medical treatments.
The primary advantage of micro moulding lies in its exceptional precision. This technique is essential for producing medical devices such as stents, catheters, and wearable sensors that must meet not only specific dimensional requirements but also stringent health and safety standards. Micro moulding achieves this by allowing the production of components with ultra-fine tolerances, often in the range of just a few microns, and it does this repeatably, there being a demand for zero failure rates in safety critical applications.
Additionally, scalability plays a crucial role in the widespread adoption of micro moulding for medical applications. Once a mold is precisely engineered, manufacturers can rapidly produce large quantities of components. The capability to scale up production means that components can be manufactured in the thousands or millions, facilitating quick distribution and significantly reducing the cost per unit. Such scalability is particularly advantageous for the production of high-volume items like medical diagnostic test strips, which require consistent quality and reliability.
Another significant benefit is the extensive customization possibilities micro moulding allows. The process can be finely adjusted to create unique geometries tailored to specific medical needs. This level of customization not only applies to the physical shape of the components but also extends to the choice of materials used, enabling the production of devices that meet exact requirements for flexibility, biocompatibility, or biodegradability. By combining these customized solutions with micro-level precision and scalability, micro moulding stands out as a transformative technology in the biomedical field, supporting innovations and improving patient care.
Impact on patient care
The miniaturization of medical devices through the use of micro moulding is significantly transforming patient care. By reducing the size of these devices, they become less invasive and more comfortable, enhancing patient comfort and potentially accelerating recovery times while minimizing the risk of post-operative complications. For example, smaller implants can be placed through less substantial incisions, minimizing tissue damage and promoting quicker healing.
Additionally, micro moulding allows for the seamless integration of sophisticated electronic components within medical devices. This advancement heralds a new era in personalized medicine, where devices are not only capable of passive tasks but can actively monitor vital signs, administer medications, and dynamically adjust their operations based on real-time changes in the patient’s condition. This capability could lead to highly individualized treatments and interventions, further improving medical outcomes and patient well-being.
Pioneering techniques and innovations
Companies like Accumold are leading innovators in the field of micro moulding, consistently pushing the limits of what can be achieved in manufacturing tiny, precise components. Accumold excels in creating micro-moulded plastic parts that are used across various critical sectors such as medical, the company utilises proprietary micro moulding techniques to manufacture parts that are not only smaller than a grain of sand but also feature intricacies that measure just a few microns across.
The sophistication of Accumold’s operations is reflected in the company’s in-house production of specialized micro tooling designed specifically for the vagaries of micro-scale production. The company also uses advanced polymers that are tailored to the specifics of a particular application, ensuring that each part meets rigorous standards of quality.
Accumold’s pioneering work in the area of micro moulding is especially significant in the medical industry, where its advancements are making way for the development of more complex, reliable medical implants and devices. This technological progress is crucial for the evolution of medical treatments and equipment, setting new benchmarks in the healthcare sector and beyond. Their ongoing commitment to innovation and excellence in micro moulding continues to open up new possibilities and applications, driving forward the capabilities of miniature manufacturing technology.
One such is the recent announcement that Accumold has found a way to micro mould thin wall cannulas in very high volumes. Micro injection moulding enables the creation of intricate and consistent cannula designs with precise wall thickness control. It eliminates the need for separate extrusion, tipping, and gluing steps by producing the entire cannula in a single mould, enhancing product reliability and reducing the risk of defects. This approach not only improves the quality and reliability of the cannulas but also offers a more scalable and cost-effective solution for meeting the demands of high-volume production in the medical industry. Micro moulding cannulas at volume with an outside diameter of 0.035” (0.889 mm), an inside diameter is 0.027” (0.6858 mm), and a wall thickness of 0.004” (0.1016 mm) is routine at Accumold.
Future directions and technologies
The future of micro moulding in biomedical applications looks highly promising, with several innovative directions that could significantly impact medical treatments and patient care. One key area of interest is the use of biodegradable polymers, which are already used in — but are poised to revolutionize — the field of implantable medical devices. These polymers can be used to create temporary implants or scaffolds that naturally dissolve within the body once they have served their intended purpose. This capability effectively eliminates the need for a subsequent surgical procedure to remove the implants, thereby reducing the overall risk and discomfort for patients.
Furthermore, the integration of nanotechnology with micro moulding represents another exciting frontier. By embedding nanoparticles or nanostructures into the moulded components, manufacturers can dramatically enhance the functionality of these devices. For instance, the addition of nanoparticles can increase the electrical conductivity or thermal resistance of the implants, which can be crucial for devices that require these properties to function correctly. Additionally, incorporating nanostructures can lend antimicrobial properties to the implants, greatly reducing the risk of infections post-surgery and during the healing process.
These advancements not only aim to improve the quality and efficacy of medical treatments but also strive to reduce the overall healthcare costs by minimizing the need for additional surgeries and by extending the longevity and functionality of implantable devices. As research continues to advance in these areas, the possibilities for new applications and improvements in micro moulding technology are virtually limitless, promising a new era of sophisticated, tailor-made biomedical solutions that cater directly to the evolving needs of patients and healthcare systems worldwide.
Challenges and considerations
Despite its numerous advantages, micro moulding also confronts several challenges. The exceedingly precise nature of this manufacturing process necessitates advanced design strategies and meticulous quality control measures to guarantee that every component adheres to the required specifications. Furthermore, the creation and integration of innovative materials and processes demand substantial investment in research and development. Obtaining regulatory approval for these new methodologies can be a complex, time-consuming, and expensive endeavour.
This requirement for continuous innovation and compliance can significantly slow down the speed to market, impacting the overall efficiency and cost-effectiveness of micro moulding projects. Additionally, the high level of technical expertise required to implement and manage these sophisticated processes can pose a barrier to entry for many companies, potentially limiting the broader adoption of micro moulding technologies in various industries. This all shows the necessity of working with an experienced and expert micro moulding innovator like Accumold which can act as your qualified micro moulding partner and help you navigate the challenges inherent in the process.
Summary
Micro moulding technologies hold a key to future biomedical advancements, offering unmatched precision, scalability, and customization for medical device manufacturing. As the technology continues to evolve, it promises to further revolutionize patient care, making treatments less invasive, more effective, and highly personalized. The ongoing developments and innovations in this field are not just enhancing existing applications but are also opening up entirely new possibilities in the medical sector.
This exploration of micro moulding technology underscores its vital role in shaping the future of biomedicine, highlighting both the current capabilities and the potential for future breakthroughs that could redefine healthcare as we know it.