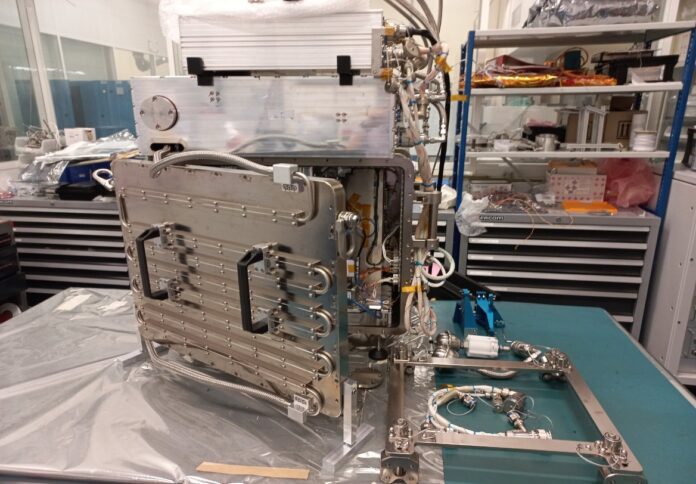
The European Space Agency (ESA) has launched the first metal 3D printer to the International Space Station (ISS).
The state-of-the-art technology, part of the Cygnus NG-20 resupply mission, aims to revolutionise in-space manufacturing by enabling the production of metal parts in the microgravity environment of space, ESA said in a news release.
“This new 3D printer printing metal parts represents a world first, at a time of growing interest in in-space manufacturing,” explained ESA technical officer Rob Postema.
He stated that polymer-based 3D printers, utilising plastic materials, have previously been deployed on the ISS, but metal printing opens up new possibilities for strength, conductivity, and rigidity in space-based structures.
Developed by an industrial team led by Airbus Defence and Space SAS, the metal 3D printer is a collaborative effort with ESA’s Directorate of Human and Robotic Exploration.
Patrick Crescence, project manager at Airbus, highlighted the significance of this in-orbit demonstration, stating, “It paves the way for manufacturing more complex metallic structures in space. That is a key asset for securing exploration of Moon and Mars.”
The 180 kg metal 3D printer will be installed by ESA astronaut Andreas Mogensen in the European Draw Rack Mark II in ESA’s Columbus module upon its arrival at the ISS.
The printer will operate using stainless-steel wire commonly used in medical implants and water treatment due to its corrosion resistance.
A high-power laser, a million times more powerful than an average laser pointer, will heat the wire to create metal prints.
The technology demonstrator will undergo a series of tests, printing four specially chosen shapes, which will be compared to reference prints on Earth.
These shapes, smaller than a soda can, will be analyzed for differences in printing quality and performance in the space environment.
As part of ESA’s goal to create a circular space economy, the 3D printer could play a crucial role in recycling materials in orbit and repurposing them for new tools or structures.
This innovation eliminates the need to send pre-fabricated tools on rockets, allowing astronauts to print necessary parts directly in space.
Tommaso Ghidini, head of the Mechanical Department at ESA, sees metal 3D printing as a promising capability for supporting future exploration activities and contributing to more sustainable space practices.
“Metal 3D in space printing is a promising capability to support future exploration activities, but also beyond, to contribute to more sustainable space activities, through in-situ manufacturing, repair and perhaps recycling of space structures, for a wide range of applications,” he stated.
Ghidini continued, “This includes in-orbit large infrastructure manufacturing and assembly as well as planetary long-term human settlement. These aspects are key focuses in ESA’s upcoming technology cross-cutting initiatives.”
Thomas Rohr, overseeing ESA’s Materials and Processes Section, added, “This technology demonstration, showcasing the processing of metallic materials in microgravity, paves the way for future endeavours to manufacture infrastructure beyond the confines of Earth.”