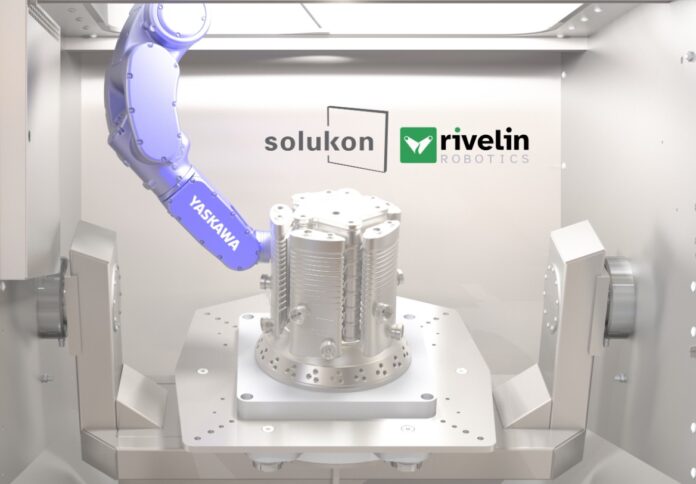
Metal additive manufacturing company Rivelin Robotics announced a strategic partnership with German manufacturer Solukon to advance automated solutions for post-processing metal and metal additive manufacturing (AM) applications.
This collaboration aims to combine the strengths of both companies to meet the growing demand for autonomous post-processing solutions in the metal AM industry, Rivelin said in a media release.
Rivelin and Solukon have identified specific areas where their expertise can be leveraged to create cutting-edge post-processing solutions.
The primary focus will be on aligning Solukon’s large automated powder removal solution, the SFM-AT800-S, with Rivelin’s precise robotic systems for support removal and finishing.
Rivelin will contribute its advanced Rivelin Netshape software and Yaskawa EU robots to enhance the capabilities of the combined system.
The development of this integrated system is driven by customer demand, as both companies have received requests from metal AM users facing unique challenges.
These challenges include the need for robotic compressed air blasting, localised and targeted vibration for depowdering large parts, robotic sensing solutions to inspect air flow in cleared channels, and various media blasting techniques for surface enhancement.
The collaborative effort will culminate in the introduction of a fully functional system at Formnext 2023, which will be held in Frankfurt from 7 to 10 November.
Rivelin and Solukon will showcase their innovative solution at the event, with booths located at stands E41 and D42, respectively, in Hall 12.0.
Robert Bush, CEO of Rivelin Robotics, expressed his excitement about the partnership and the upcoming showcase at Formnext, saying “This isn’t just another trade show for us; it marks a year since we debuted, and we’ve made some significant strides.’
“Our Rivelin NetShape Robots have gone from blueprint to reality, and alongside Solukon, we’re crafting automated solutions for post-processing metal AM parts—exactly what the industry’s been calling for. It’s all about delivering real value, and we’re doing it in spades,” Bush noted.
Meanwhile, Andreas Hartmann, CEO/CTO at Solukon Maschinenbau, highlighted the increasing complexity of internal channels and cavities in parts as a trend in additive manufacturing.
He mentioned that aerospace customers, who often work with challenging materials like copper, have high requirements for automated depowdering.
“With programmable rotation, targeted vibration and thanks to our SPR-Pathfinder software without any human programming efforts, we also get the aerospace parts powder-free with our Solukon technology in a reliable and repeatable way,” Hartmann said.
He added, “A very useful task for an integrated robot in our SFM-AT800-S is a channel cleanliness check with blowing or the removal of powder deposits from the surface of the components. We are very glad to have found this experienced partner for automated finishing in Rivelin.”