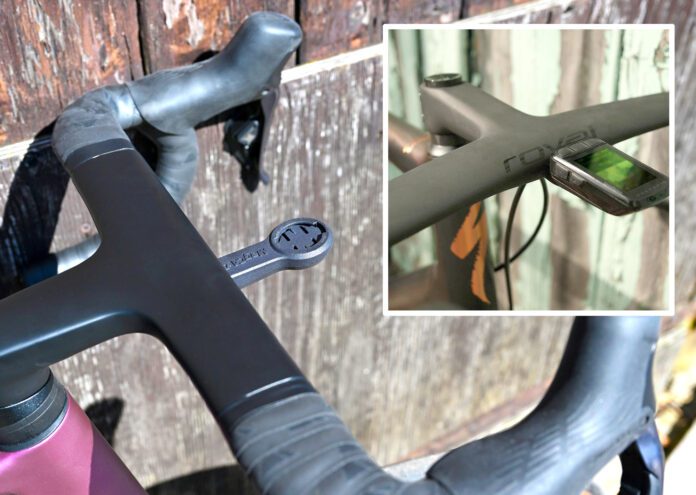
In recent years, the cycling industry has undergone an immense transformation, owing mostly to the adoption of cutting-edge technologies. One of these technologies, 3D printing, has played a significant role in allowing companies like MagCAD to revolutionise the sector through customised solutions and products.
In a case study, London-based 3D printing company 3DPRINTUK stated that bike designers have always worked around international standards and the commonality of parts. However, over the past decade, there has been a shift away from this as brands look for better system integration, distinctive selling characteristics, and ever-shrinking marginal advantages.
MagCAD Designs Ltd, directed by Andrew Magnier, a former British National Track Cycling Champion and MEng Aerospace Engineer, highlighted how 3D printing played a central role in their business and how 3DPRINTUK aided in setting new standards in their production.
MagCAD business model and 3D printing an ideal match
Andrew Magnier explained in the paper how 3D printing methods support the MagCAD business model rather than alternative manufacturing processes. According to him, 3D printing is critical to the business model because it allows the Staffordshire-headquartered firm to respond rapidly to new opportunities, emphasising that the technology can build, test, and validate components in a much shorter time frame.
“For production, though, it reduces our upfront investment — both in terms of time and cost — compared with more traditional manufacturing methods. It also allows us far greater design freedom for creating complex geometries that are not then subsequently restricted by tooling and traditional manufacturing considerations,” Magnier explained.
How MagCAD manufactures parts and products for its clients
Magnier offered some insight into how MagCAD operates and serves its clients by producing a variety of parts and products for them. He stated that they will be approached with a design request by a cyclist, cycling brand, or bike shop, and these are typically criteria for attaching smart gadgets such as GPS computers, lights, and cameras to parts of a bike such as the handlebars.
“We will always assess the feasibility of each request before making a commitment to develop parts. When we first started out, we would tackle most requests but as the business has grown, we have had to become far more selective as we now receive hundreds of design requests every week,” he noted.
With a growing portfolio of over 350 different designs, it is critical that they can scale up batches to over 100 items each order, and having 3DPRINTUK as their production partner allows them to do so quickly. Magnier explained that several parts have complex locking interfaces and overhangs, and typically, these design elements cannot be manufactured in a single piece via injection moulding.
“Sometimes our customers will spot opportunities to use existing designs in a slightly different way and we’re able to make the necessary changes very quickly. That’s one of the key strengths to the 3D printing process,” the MagCAD official stated.
Enabling on-demand production for SMEs
Magnier further said that as MagCAD has grown, they have seen spikes in demand for specific products, implying that they can quickly sell out of things in good supply. He said the company can respond to demands because of the ability to reproduce parts rapidly and reliably.
The 3D printing technique, and more specifically the industrial systems at 3DPRINTUK, allows the firm to simplify and optimise the design, minimise post-manufacturing assembly processes, and cut time and costs,” he added.
“All of this benefits our customers as we can pass these time and cost savings on to them,” Magnier noted.
SLS 3D printing and quality control
The selective laser sintering (SLS) 3D printing method from 3DPRINTUK is what MagCAD mostly uses in terms of the strength and quality of the products. According to Magnier, the material and method give an excellent mix of strength and stiffness, making them trust the parts that are created.
He also said that MagCAD places a high importance on quality control, which is highly compatible with the principles of 3DPRINTUK. “MagCAD has a number of processes in place to ensure the level of quality we maintain is particularly high and it’s great to see 3DPRINTUK also prioritise quality as much as we do. Every single component that’s sold directly by us is tested before it’s shipped,” he noted.
Magnier discovered 3DPRINTUK in 2020 while looking for a UK-based 3D printing service provider in anticipation of the potential disruption created by Brexit.
Summing up the collaboration, Magnier commented: “We’ve always found the support received from the 3DPRINTUK team to be outstanding. We are able to share knowledge, ask technical questions and get prompt answers to queries.
“Business is two-way and it’s critical that our expectations are aligned with the 3DPRINTUK team for a successful working partnership, which they are. Working with 3DPRINTUK is a pleasure and we’re very excited to see where we can take the partnership in the near future,” he concluded.