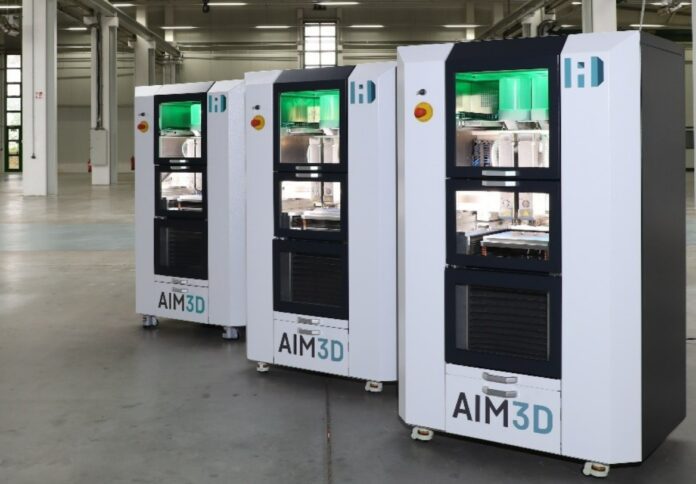
The University of Rostock and metal construction company Stenzel MIM Technik have collaborated to create a 3D-printed metal injection mould (MIM) with AIM3D’s CEM technology on an ExAM 255 system in a push to combine high accuracy and production speeds.
The partners are working on a MIM tool employing 3D printing and integrated, near-contour cooling as part of a project financed by the German Federal Ministry of Economic Affairs and Energy, AIM3D said in a press release.
“Composite Extrusion Modelling (CEM) by AIM3D is an additive manufacturing process that uses feedstocks consisting of plastic binders and metal powders known from metal injection moulding (MIM),” explained Dr Abdullah Riaz, research associate at the Chair of Microfluidics at the University of Rostock.
He said, “With this process and after the necessary debinding and sintering steps, complex metallic components can be rapidly produced.”
The project, to be completed by October 2023, uses helical cooling channels directly in the mould to significantly minimise cycle time by cooling near the contour even during the cycle.
The intricate shape of the cooling ducts is made possible by CAD technology, and long-term studies suggest a 20 per cent decrease in cycle time.
Compared to traditional processes, which may take up to eight weeks, AIM3D said the 3D approach can potentially cut manufacturing time to only five days.
An optimised 3D model of the mould has also already been developed and transmitted to the ExAM 255 CEM system.
The company said the “green part” is now printed before being sintered in multiple processes to acquire the final material qualities.
Complex metallic components may be created quickly using this technology following the appropriate debinding and sintering procedures.
Simultaneously, the CEM method enables control of the volumetric shrinkage associated with sintering.
The component is a thick-walled part with narrow fins that cannot be manufactured without near-contour cooling because they are challenging to mould.
Stenzel MIM Technik hopes to achieve a significant reduction in cycle time for this component by up to 70 to 80 per cent. However, injection moulding trials for testing are still pending.
AIM3D underscored that the multi-material 3D printer ExAM 255 can be used with various materials such as metals, plastics, and ceramics as well as with various processes including hybrid components.
Systems utilising the CEM method produce tensile strengths comparable to those of conventional thermoplastic, mould-bound injection moulding, as compared to powder bed technologies or even other 3D printing techniques that utilise filaments.