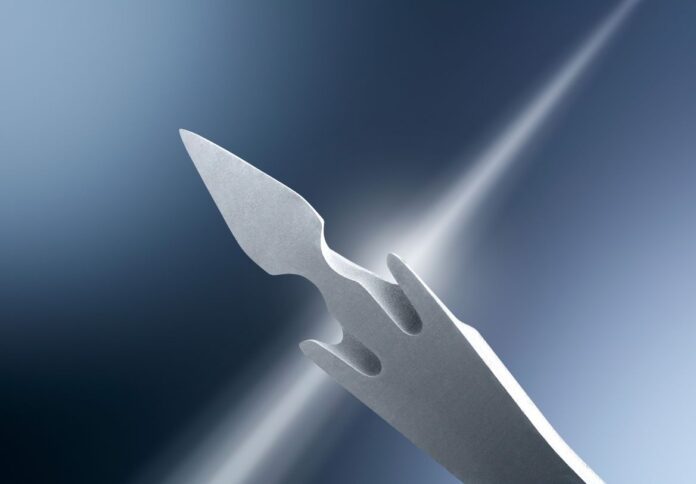
Photo-chemical etching (PCE) company micrometal has successfully showcased the capabilities of its next-generation precision metal processing technology following some recent work with a manufacturer of ophthalmic devices incorporating surgical blades.
Jochen Kern, head of sales and marketing at micrometal, said the customer commended the blade produced through PCE, describing it as “the sharpest they had ever seen.”
According to micrometal, PCE is capable of delivering significant benefits to the production of intricate blades for eye surgery, such as allowing the creation of extremely precise and intricate blade designs with sharp edges and tight tolerances.
The process enables manufacturers to ensure the highest level of accuracy and consistency during surgery, which are highly important in eye surgery, where even small variations in blade design can have a significant impact on patient outcomes. It also allows the production of extremely thin blades, down to a few microns in thickness, with no burrs or rough edges to ensure smooth and precise cutting.
PCE is a chemical, non-contact process, which means there is no physical force applied to the metal during the manufacturing process, reducing the risk of deformation or damage to the blade.
Kern said micrometal’s next-generation PCE is the go-to technology for manufacturing intricate metal parts for several reasons, including unparalleled precision and its capability to create geometrically complex designs and shapes with tight tolerances that would be difficult or impossible to achieve with traditional manufacturing techniques.
In a press release, micrometal explained that it has taken what is already a precise technology in PCE and enhanced it, allowing it to produce extremely small features the size of as little as 25 microns.
The next-generation process uses a unique and patented wet paint etching system, with the coat measuring 2 to 8 microns thick, compared to traditional dry PCE coating, which is 10 to 50 microns thick.
micrometal’s next-generation process can achieve a minimum hole diameter of 80 per cent of the material thickness and single-digit micron tolerances are attainable repeatably.
“PCE produces a very smooth and sharp cutting edge compared to conventional mechanical grinding of similar blades. Under a microscope, mechanically sharpened edges show fracturing and rough edges due to process issues and ‘brittle’ material conditions from work-hardening. micrometal’s combination of liquid photoresist and high-resolution tooling produces an extremely sharp cutting edge that does not ‘tear’ tissue,” Kern said.