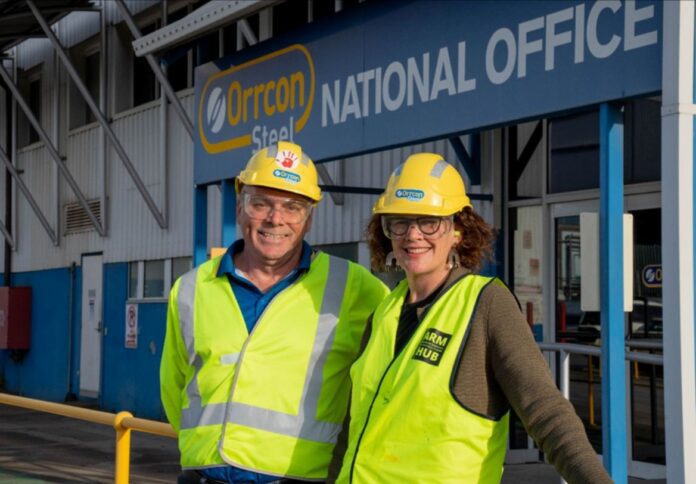
Media Release by ARM HUB
In a difficult market where resourcing, supply chain issues and energy costs are the immediate priority for many manufacturers, Orrcon Steel’s General Manager Tony Schreiber is investing in the future: AI and robotics.
“Success for our business, isn’t really about next financial year; it’s really about 2030 and beyond,” Mr Schreiber said.
“How do we position the company now so that by the time 2030 comes along, there’s different leadership, capability, customers, and market opportunities – that is, what we should be doing now, so that we will be well credentialed to be a supply chain partner in the future.”
Orrcon Steel, a leading Australian steel manufacturing and distribution company with 750 employees and two manufacturing sites in Salisbury, Brisbane, and O’Sullivan Beach in Adelaide, recently renewed their platinum membership with the Advanced Robotics for Manufacturing (ARM) Hub.
ARM Hub CEO Associate Professor Cori Stewart said ARM Hub was delighted to continue its platinum level membership with Orrcon, on a range of initiatives.
“Our collaboration includes optimising Orrcon’s steel coil slitting operations and embedding a data science researcher at their Salisbury site to futureproof steel production operations,” Dr Stewart said.
Mr Schreiber said Orrcon would benefit from tapping the technical talent that ARM Hub provided through its extended network of robotics and AI expertise from universities.
“It’s not so much ‘upskilling’ – it’s more about right-skilling the organisation for the way that society’s evolving,” he said.
“It doesn’t really matter what we’re after, whether it’s quality, service, cost improvements, or whether it’s just being able to attract the next generation of employees – we’ve got to innovate.
“We’ve got to automate, we’ve got to roboticise ourselves, but we’ve got to do it in a way that takes everyone along for the ride.”
Mr Schreiber said one of the key focus areas of the ARM Hub partnership was Orrcon’s slitter equipment which takes 26-tonne steel coils and slits the steel into the required width, and then shapes that into a tube.
“That slitting operation makes or breaks the tube-making operations, and what really governs the efficiency of tube-making is the quality of the slit edge.”
ARM Hub experts used AI to identify the most effective means of maximising the performance of the slitter, in terms of yield optimisation, run speed, labour productivity, waste minimisation and workforce safety.
“The insights that we got from that are going to feed into our improvement programs in the financial year 2023 and beyond,” Mr Schreiber said.
In another innovative project, a QUT data science expert is analysing 10-years’ worth of dispatch and production data to identify ways of optimising the production schedule of Orrcon’s three tube mills running at their Salisbury site.
“The output of these three mills, in terms of volume, is highly dependent on product mix, run lengths, change-over time optimisation, and the cubic metres of the finished product,” Mr Schreiber said.
“There can be swings of 20-30 percent of daily output, just depending on the product mix that’s being made on each one of those mills.”
The modern steel industry has been the cornerstone of global industrial economies since the late 1850s, and Mr Schreiber sees major opportunities as economies shift to renewable energy production.
“With the support of ARM Hub, we are looking at how we best position the business to be a well-credentialed supplier to the needs of the renewable energy sector,” he said.
“In terms of scale, if the hydrogen industry is fully supplied via renewables by 2050, our calculations are that just the solar farm area alone will consume land banks equivalent to Geelong through greater Melbourne, and down through the Mornington Peninsula – just to supply electrolysers for the hydrogen industry.
“There is going to be a significant demand for steel products and the services our company offers.”
Mr Schreiber said traceability was another issue the company was focused on.
“Traditionally, traceability has been about quality assurance for us but now the industry is moving to traceability through supply chains, so the end user has all the information on compliance and how the material has been transformed.
“And, if you look at the experience of the last two years with all the supply chain disturbances –many people are rethinking whether they are content to continue with longer lead time supply chains.
“Most of our customers are moving towards shorter supply chains. As we develop down that path, intimate knowledge of where every piece of inventory is, at every point in time, is not only a business advantage, but it’s a competitive advantage.”
Mr Schreiber said the biggest focus for Orrcon was to ensure staff do not feel they are being left behind by technology and automation.
“There will always be a critical need for human involvement in manufacturing. What we are trying to do is optimise what we can optimise, and amplify the knowledge that’s in our people, to bring the business more success and hopefully give our staff great careers along the way.”