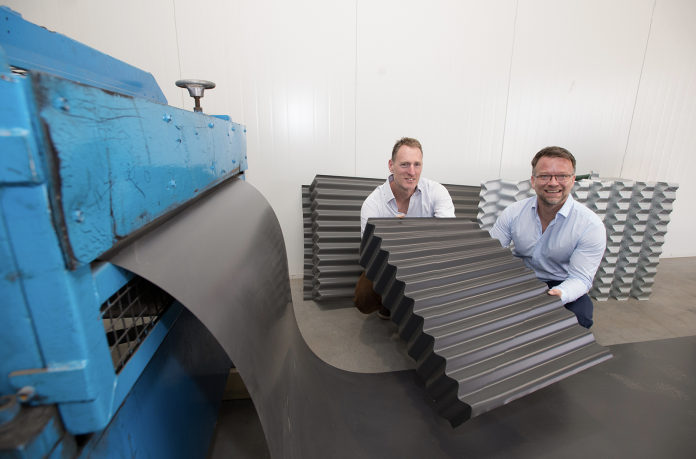
Media Release By FormFlow
Geelong manufacturing start-up FormFlow and Deakin University have successfully concluded a research collaboration with outcomes delivering new commercial solutions for the steel forming industry.
The project, supported by the Innovative Manufacturing Cooperative Research Centre (IMCRC), was designed to establish an Industry 4.0 manufacturing cell to control and optimise FormFlow’s corrugated steel bending process.
However, while undertaking fundamental research into the solution, the project team identified additional outcomes that would deliver greater efficiencies.
The first is a 2D laser system that monitors the cross-sectional shape of sheets before and after bending and enables the manufacturer to perform continuous quality control. The second is an Industry 4.0 manufacturing cell capable of producing a corrugated corner bend from a flat sheet of steel.
Matthias Weiss, Senior Research Fellow at Deakin University, said having the flexibility to adjust the scope of the project enabled the team to develop completely unexpected, but more effective, solutions.
“Our research still focused on creating a high-volume manufacturing cell, but instead of implementing equipment to monitor and control the bend, we designed a new technology and forming process called the in-phase continuous corner (IPCC),” he said.
“IPCC means we no longer need to compensate for differences in steel corrugations or work with fixed lengths. We can instead take a flat steel sheet and form an easy-to-install bend in continuous lengths.”
Dr Matthew Dingle, FormFlow’s Managing Director, said industry had already shown significant interest in both products.
“Roll forming manufacturers are looking to FormFlow’s 2D laser system because it enables continuous, real-time quality control. The laser automatically measures the key parameters of the steel and provides the necessary data, something that is currently a manual, time consuming process,” he said.
“The project outcomes have also contributed to our FormFlow Living business, which designs, develops and manufactures high-value, affordable modular housing using innovative building systems.
“To scale up FormFlow Living’s delivery model, we will soon offer the building systems to customers under license and are also establishing our first regional manufacturing hub in South West Victoria later this year.”
Dr Matthew Young, Manufacturing Innovation Manager at IMCRC, congratulated FormFlow and Deakin on the successful completion of their research collaboration.
“By starting with the research fundamentals, FormFlow and Deakin were able to justify their non- traditional approach to problem-solving and develop products of significant benefit to Australia’s sheet metal manufacturing industry,” he said.
“Once commercialised, FormFlow’s groundbreaking smart technologies will help standardise and validate suppliers’ material inputs and FormFlow outputs, creating affordable, high-quality products with minimal waste.”
Image Supplied: formflow.net.au