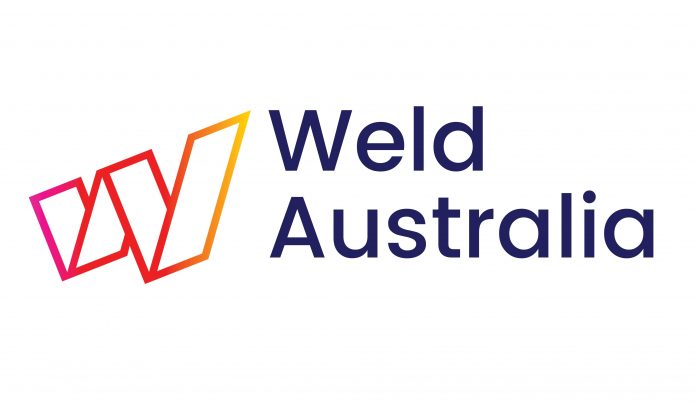
Media Release by Weld Australia
Manufacturing is a key contributor to the Australian economy. According to the Federal Government’s Australian Manufacturing Performance Report, manufacturing contributes $100 billion to the Australian GDP every year, employs around 1 million people, and is responsible for an astounding 26% of all business expenditure on R&D in Australia.[1]
This strength of performance is made possible by Australia’s world-class local manufacturers. Australian manufacturers are helping to deliver a strong, resilient economy for all Australians, which is more important than ever in the post-COVID world. Australian manufacturers deserve to be backed by our Governments.
According to Weld Australia CEO, Geoff Crittenden, “Australian manufacturing is world-class. We need our Governments to recognise that local manufacturers, fabricators and welders have the capability and capacity to deliver their local asset and infrastructure needs. Government procurement decisions must prioritise Australian manufacturing.”
Weld Australia is calling on Governments to have confidence in Australian manufacturing in the wake of several faults in New South Wales’ trams and ferries.
All 12 trams that normally run on the Central to Dulwich Hill line were decommissioned last month. Major cracking was found in the trams, which were manufactured in Spain. The trams only came into service in 2014 and are already out of warranty, which means New South Wales taxpayers could be liable to foot the repair bill.
This was quickly followed by the suspension of the Newcastle light rail after a mechanical issue was identified in the trams, which were built by the same Spanish manufacturer behind the Dulwich Hill fleet.
A number of cracks were also recently discovered in the hull of one Sydney’s new Manly ferries. An independent report identified several welding defects onboard the Balmoral—one of the Emerald-class ferries, which were built in Indonesia and China.
Weld Australia CEO Geoff Crittenden said, “Australian manufacturing, fabrication and welding companies are globally competitive and more than capable of delivering infrastructure like Sydney’s trams and ferries on time and, more importantly, in accordance with all relevant international Standards.”
“Over the last few years, the Australian fabrication industry has made enormous progress. In 2018, there were just 15 local companies certified to the international Standard for welding quality. Today, there are over 75 companies certified by Weld Australia as compliant with the Standard. Several local companies are also certified to the international Standard for welding rolling stock, while still more have passed the most stringent welding certification available—the German Standard for welding of armoured vehicles.”
“Working with TAFEs nationally, Weld Australia has helped rejuvenate technical welder training in Australia, so that it is now among the most advanced in the world. Many of our TAFEs boast Advanced Welding Training Centres that feature state-of-the-art augmented reality welding simulators. Here at Weld Australia, we continue to deliver training in accordance with the internationally recognised Standard for Welding Supervisors, Inspectors and Engineers—our enrolment numbers have more than doubled over the last three years,” said Crittenden.
“Given all this, it should come as no surprise that Australia is home to some of the world’s most high-quality, high-tech manufacturers, from Bombardier (now known as Alstom) who manufacture trains and trams in Melbourne, through to Austal who is one of the top ship builders in the world.”
“Australian Governments have responsibility for ensuring that public assets and infrastructure are safe and reliable. Their procurement policies must take into account the ‘whole of life cost’. The cheapest upfront cost is not necessarily the cheapest whole of life cost. Nor is it the most reliable and safe for the public.”
“Australian fabricators are not only trained and certified to the highest international Standards—making them more than capable of manufacturing our assets and infrastructure—but because they are locally based, it is easy for Government engineers to verify their processes and quality.”
“This type of ongoing verification by Government engineers is used by the Department of Defence for all defence projects. Similarly, Transport for New South Wales employs this process for every bridge constructed in the state. Every piece of infrastructure is quality checked throughout the manufacturing and installation phases. There is no reason why State Governments couldn’t do the same for assets like trams and ferries—they just need to award the contracts to local suppliers.”
“We need a commitment from our Governments to increase levels of local content for all procurement decisions. We need to bring home the manufacture of goods like trams and ferries. There really is no reason for our Governments not to onshore this manufacturing work—Australian manufacturers are ready, willing and more than capable,” said Crittenden.
[1] https://www.industry.gov.au/publications/australian-manufacturing-performance-report