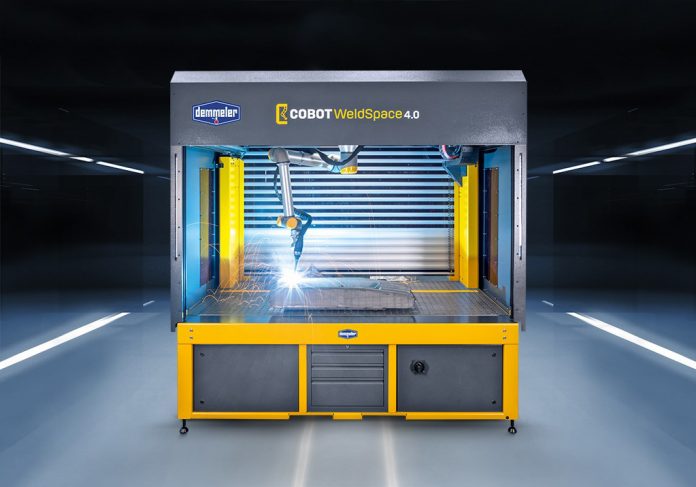
Media Release by Leussink
Leussink, the exclusive Australian distributor of Demmeler 3D Welding table solutions, has expanded its range with the new Demmeler WeldSpace system, a fully equipped welding cell with a built-in welding cobot.
Leussink’s Managing Director Jason Leussink says the new Demmeler WeldSpace system is ideal for small and medium-sized companies with moderate production volumes.
“Like other cobot (collaborative robot) systems, the WeldSpace can significantly increase productivity levels. The cobot works alongside humans, taking on dull, repetitive tasks, reducing human error, and allowing humans to be more productive with other, more valuable tasks.
“By using cobots, manufacturers lower their cost of production while increasing profitability. Humans can utilise cobots as a tool to ensure accuracy and consistency in their work, while minimising downtime in a manufacturing plant,” said Leussink.
The intuitive user interface of the Demmeler WeldSpace programming and operating concept (DWSP) for operating the cobots makes it straightforward for employees without programming knowledge to easily learn to control the robot.
Developed by Demmeler’s welding experts the software is adapted to the robot and welding process. The cobot can be moved by hand to the place where welding is to be started and stopped. Intermediate waypoints and sections are also programmed. This allows the operator to create professional welding programs with the touch of a button. The welder has full access to the relevant functions of the system with only one control panel.
The Demmeler WeldSpace cell has two very large and easily accessible working areas – Space A and Space B with a length of approximately 2,400 mm in the standard version and requires very little floor space. It even has indentations for the forklift forks. The enclosure opens on both sides (roll-up doors) and automatically moves from the front to the rear work area.
Being a modular system, it can be set up and used in many ways. For example, while the robot welds on one side, an employee can set up and reclamp on the other side in parallel. Utilising a partition wall, this can be divided even further, thus creating a third workstation. There are four different options for extraction.
The optional manipulator can move a workpiece independently by up to 360 degrees so that there are no blind spots when machining it.
To learn more about the COBOT WeldSpace 4.0 from Demmeler visit https://www.youtube.com/watch?v=153xrDZ6-6s&t=9s
As well as the new WeldSpace, the Demmeler welding table is an ideal partner product for a cobot. Versatile and durable, the Demmeler 3D workbench and welding table is suitable for all types of welding and fabrication work and can be set up easily and precisely for a cobot.
Cobots can be anchored and fixed to a Demmeler table system to ensure accuracy and versatility, with the cobot able to return to the same position every single time.
“Working in partnership with robotic experts, we develop cobot-based systems for clients in a range of industries, enabling them to meet many different requirements. One of our customers – a smart automation and robotic solutions business – packages its cobots with the Demmeler modular fixturing tables from Leussink as a collaboration system for its customers.
“At Leussink we don’t just sell a welding table and walk away. We work with our clients to make sure the Demmeler welding and fabrication system works for them by tailoring a solution to their needs, and providing onsite visits, training sessions, and a wide range of accessories.
“Through our knowledge and decades of experience, Leussink can create welding and fixturing solutions for the Australian market that stand the test of time. We work with our customers to capitalise on efficiencies and productivity, without compromising quality and accuracy,” concluded Leussink.