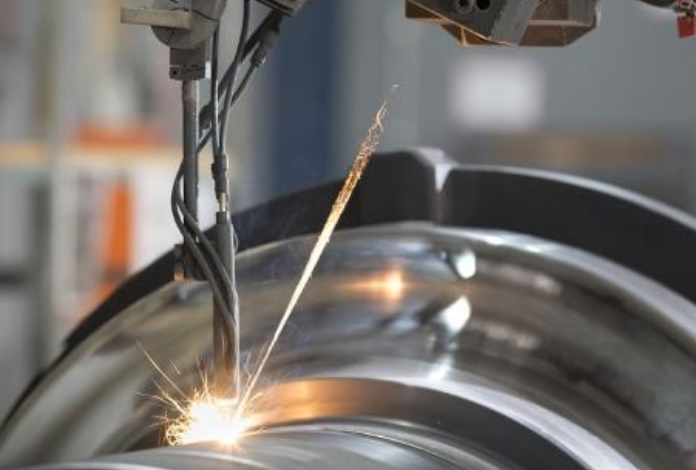
Media Release
In a new $2.4 million research partnership between the University of South Australia, LaserBond, and the Innovative Manufacturing Cooperative Research Centre (IMCRC), experts are set to develop some of the world’s most resilient minerals processing equipment.
LaserBond, a pioneering Australian surface engineering company and the University of South Australia’s specialist Coatings Research Group at the Future Industries Institute, continue their fruitful collaboration on a new challenge.
Minerals processing machinery, often worth hundreds of thousands of dollars, endures some of the harshest possible conditions – erosion, corrosion and wear and tear induced by repetitive impact.
A key competitive advantage for the industry and for manufacturers would be to increase the longevity of mineral processing equipment through composite coatings (called cladding).
The improved cladding needs to match facility maintenance shutdown schedules. By matching the machinery life to service schedules, unforeseen shutdowns can be avoided or minimised. Shutdowns for repairs and maintenance of the equipment can cost more than $100,000 for every hour of downtime.
UniSA lead researcher Professor Peter Murphy, says he welcomes the chance to grow the advanced manufacturing sector within Australia.
“This comes at a time where we need to nurture our manufacturing capability and this project has the capacity to grow, employ and lead Australia through the challenging economic times,” Prof Murphy says.
Key researcher on the project, UniSA’s Industry Associate Professor Colin Hall says industry experts in surface engineering, such as LaserBond, have long recognised the challenge and have specialised in the development of hard, wear-resistant coatings using laser cladding.
“What we hope to do through this partnership is work with LaserBond to refine the technology, specifically focussing on key areas within mineral processing machinery prone to wear in different circumstances, to provide tailor-made coatings that resist that degradation,” Assoc Prof Hall says.
“UniSA’s extensive tribology laboratories can be used to perform accelerated wear testing in erosion, corrosion and impact abrasion, and we want to combine these results to predict wear rates in the real world and then inform material and process optimisation carried out by LaserBond.”
CEO and Managing Director of IMCRC David Chuter says the research collaboration builds on a long-standing and collaborative partnership between LaserBond and the University of South Australia.
“Together, wear and corrosion, continues to be a costly and disruptive challenge across many industries and developing advanced materials and technologies for wear and corrosion protection will help both Australian and global manufacturers combat these challenges,” Chuter says.
“It is great to see, that through engagement with the University of South Australia’s researchers, LaserBond, in collaboration with local manufacturers can develop its solution locally and then take it globally.”
Image credit: www.unisa.edu.au