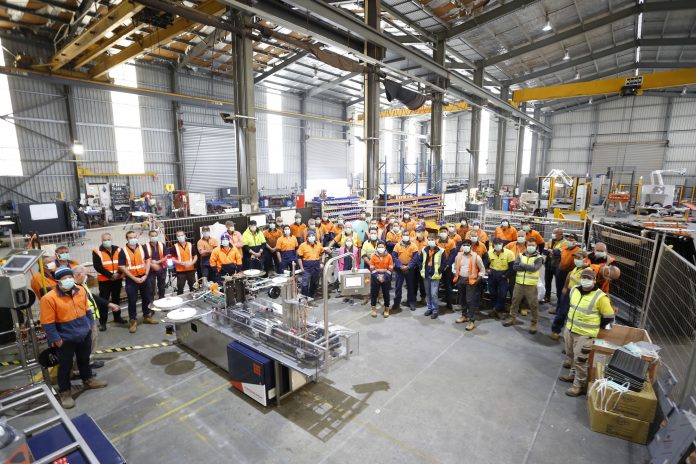
Article by Rod Hunt, Head of Customer Strategy and Innovation at Autodesk (Australia & New Zealand)
When Autodesk customer Foodmach, an automation, robotics, integration and turnkey project company located in Victoria’s Shepparton, was asked to deliver seven mask-making machines in just 60 days for Project Med-Con to keep up with demand during the pandemic, it was technology that supported them in achieving their goal. Until recently, Med-con was Australia’s only surgical mask manufacturer and was tasked by The Department of Industry, Science and Technology to increase its mask production quickly from two to 50 million masks per year during COVID-19.
Foodmach’s objective was to recreate life-saving machines that were designed and manufactured 40 years ago, however they had a few obstacles to overcome:
- Original drawings didn’t exist, so the machines had to be reverse-engineered: usually a timely process that involves a lot of testing and adjustments
- Original parts were obsolete
- They hadn’t built mask-making machines before; and
- They had just 60 days to make it happen in the middle of a pandemic.
Foodmach was given eight weeks to get the first machine ready for testing; they did it in six. They had two weeks to get the first machine up and running at Med-Con, but managed to do it in just one day. As a result, Med-Con started mask production on its first new machine almost a month ahead of schedule.
Transitioning to 3D modelling transformed the Foodmach business and supported them in meeting their Med-Con goal.
The Foodmach team found that the use of Autodesk Inventor/Vault and other ERP systems showed a 30 percent increase in productivity in creating mask-making machines. More specifically, the 3D technology enabled the team to have multiple engineers working on the project at once. Through Autodesk technology, the Foodmach team was able to quickly share their solid models across their east coast offices, so that the entire team – from their Computer Numerically Control (CNC) machinists to their salespeople – could be involved in design and manufacturability reviews. This significantly reduced rework, creating a more sustainable outcome.
Foodmach now has a complete bill of materials – everything they need to build the machines, including where parts are from, the details, process, suppliers, how many are needed and more. Prior to using Autodesk technology, this was all done manually and there were big opportunities for errors or omissions. This meant that previously, it took one week from design to manufacture, but now Foodmach can do it in minutes.
Professional-grade 3D technology provides powerful efficiencies and has capabilities for engineers that will support them in delivering projects at a level that previously couldn’t be achieved. We are excited to see this technology being taken up by innovators like Foodmach who are using it to create positive change in the world and supporting others through initiatives like their mask-making machines.