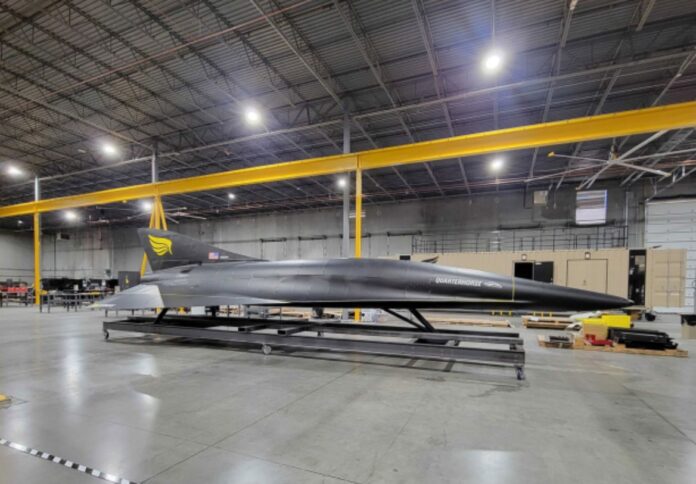
Defence organisations in the United States and the rest of the world are under increased pressure to maintain their competitive edge by examining the most recent technology developments as the balance of power shifts and pressure grows.
Thus, the defence industry must use all of its resources to advance military innovation, and metal additive manufacturing (AM) offers a special chance to do so.
Having the potential to completely transform the defence sector, the method can support and sustain current, ageing infrastructure while also enabling a future of extremely sophisticated, innovative technologies.
In a blog article derived from a whitepaper titled, “Maintaining Battlefield Superiority with Metal 3D Printing,” Velo3D examined five ways that sophisticated metal AM can revolutionise the defence sector.
Maintaining legacy equipment
Looking ahead and keeping up with competing world powers is undoubtedly a crucial motivation for our defence sector, but it does not address the immediate challenges of servicing ageing assets and infrastructure that may not be modernised in the near future.
Advanced metal AM supports the most difficult maintenance and sustainment challenges by providing a reliable source of parts to extend the life of existing assets and respond to shifting maintenance and sustainment challenges with speed and precision.
The use of modern metal AM can address sustainability issues by giving a reliable source of parts to increase the lifespan of current assets. The article states that cutting-edge metal AM techniques like the one that was invented by Velo3D can be used by US defence organisations to print components without redesigning them.
Supply chain agility improvement
The pandemic has revealed how fragile and inadequate manufacturing supply networks really. Thus, navigating supply chain choke spots that cause delays of several months is a significant challenge for parts that are essential to operations.
The article states the defence sector can significantly shorten lead times for crucial parts by switching part manufacturing to modern metal AM technologies.
The defence industry can use a vast network of contract manufacturers to build a distributed supply chain that demonstrates the flexibility required to keep up with any developing global war rather than depending on single sources of production.
Advanced metal AM improves competitiveness
According to the article, the defence industry can execute complex parts, notably in the critical field of hypersonics, by using advanced metal additive manufacturing, which goes far beyond the restrictions of traditional production techniques as well as legacy metal AM equipment.
For instance, Aerojet Rocketdyne and nTopology collaborated to use Velo3D’s fully integrated metal AM solution to create lighter, smaller rocket control systems.
These part improvements result in greater efficiency and fuel consumption, longer lifespans due to more robust material selections, higher pollution regulations, and more.
Repeatable production of key components in near-theatre operations
Getting one machine to replicate a product exactly the same as the machine next to it has been a barrier to metal AM being a dependable, scalable manufacturing option.
Scalability has been made possible with modern, cutting-edge metal 3D printing systems, like the one Velo3D invented, through the integration of design software, printing hardware, quality assurance, and fleet-level calibration.
According to the article, one advantage of using metal 3D systems in military applications is that manufacturing centres may be established up near-theatre to send critical parts to the front lines nearly on demand.
Having less dependency on foreign manufacturing
Lastly, the article states the establishment of advanced metal AM manufacturing aids in maintaining tactical advantage.
This can be done by providing an on-demand replacement component manufacturing system that reduces dependency on foreign parts production and requires less specialised labour to run.
Velo3D said the defence sector may collaborate with dependable partners and support US economic growth by using American contract manufacturers.