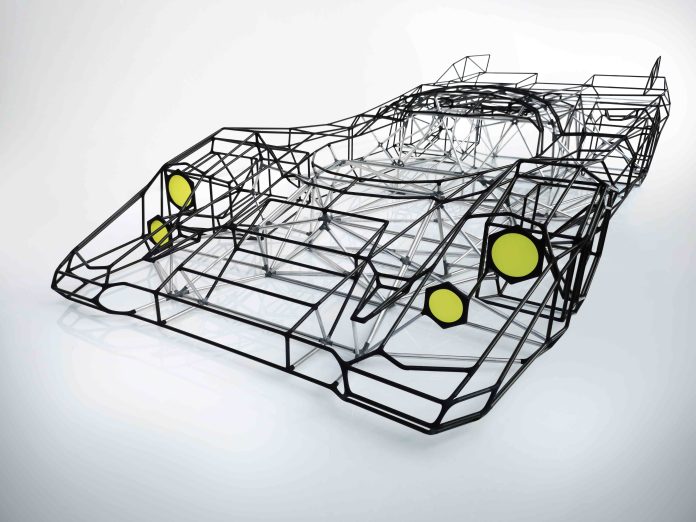
Article by Nick Allen, Managing Director, 3DPRINTUK
The uses of 3D printing today are well established across industry, and it is routinely used as a prototype and production technology. As more and more companies become aware of the design freedom that 3D printing stimulates, and the versatility of the technology when it comes to creating innovative parts and components, its adoption by a whole host of designers and manufacturers is burgeoning.
Occasionally, however, the use of 3D printing has the ability to stop you in your tracks, and such is the case when looking at the work undertaken by Jonny Ambrose. Ambrose makes hugely imaginative and tactile automotive sculptures, and for the last five years or so, 3D printed parts have been at the heart of his work.
Ambrose says, “What makes my automotive sculptures work is the juxtaposition of traditional techniques such as steam bending of wood alongside the use of ultra-up-to-date manufacturing processes such as CAD solid modelling and 3D printing. Whereas previously I would use milling when trying to create lattice structures, for example, today I use 3D printing which is able to build strong, lightweight structures with geometries impossible to achieve using traditional manufacturing methods.”
Ambrose has been working with 3DRPINTUK for a number of years since recognising the ways in which 3D printing could be incorporated into his work. Lattices are an ideal example of how 3D printing opens up design possibilities. What makes lattices unique is how they lay out materials into design elements to form an ideal structure that are made up of micro-architectures with a network of nodes and beams or struts. This format dramatically reduces weight while retaining structural integrity and giving a larger degree of control over certain characteristics. These interlinking portions can enhance various areas of performance and use less material without weakening the object or compromising its integrity.
The largest one-piece lattice that Ambrose has produced was 40 cm long, and this demanded that the team at 3DPRINTUK used all their know-how and understanding of 3D printing to accommodate the piece in the build chamber, and ensure its integrity once built. This was all about orienting the part correctly to get the best print definition, and making sure that there were no peripheral distortions at the extremities of the part.
For Ambrose, 3D printing has opened up a plethora of possibilities for using lattices in his work, but that is not all that the technology allows. He says, “Beyond the creation of lattices per se, I use 3D printing because I like the aesthetic of some of the polished finishes. Also, it allows me to create more intricate shapes and features which would not be feasible for me to do by hand. I find the aesthetics of parts produced via selective laser sintering (SLS) or via Multi-Jet Fusion (MJF) extremely attractive, and it complements the woods, metals, or carbon fibre I use in many of my works. For me, 3D printed parts are just another material, but a material that brings new elements to my works that I cannot achieve via alternate means.”
Ambrose came into contact with 3DPRINTUK at a trade show when he was researching the state of the 3D printing sector and whether the technology was something that he could incorporate into his work. Initial projects tinkered around with the technology often building simple solid parts that could have been milled, but which through the use of 3D printing and Autodesk’s Fusion 360 software facilitated a relatively simple and seamless workflow. Over time, Ambrose has used both the SLS and MJF processes through 3DPRINTUK, and also an array of post-processing technologies as he creates more and more intricate parts.
“I use polishing to add the required aesthetic to some parts. I find that polishing gives the parts produced a nice patina-like effect especially on the black parts but to an extent on white parts as well. While on occasion I use unpolished parts where I require the almost ‘sugar lump’ aesthetic, where you can see the grain, it is more often than not nice to have control over the smoothness of parts, and I especially like the almost slate like appearance that can be achieved on polished black MJF parts,” Ambrose comments.
Ambrose has been working with 3DPRINTUK since before the company introduced its upload portal and ordering interface, which has more recently transformed the way that he uses the technology.
Ambrose continues, “I have to say that I love the ordering interface and file upload portal at 3DPRINTUK. Above all, its, easy-to-use. You simply drag and drop files, and you have the ability to track everything and see how an order is progressing. Also, I can get into the system and edit part details if needed. It just works, and is very well thought out. It makes the customer’s life easier, and is obviously designed with the ultimate customer experience in mind. I love being in control of my projects and getting all the cost and time-of-build feedback automatically without the intervention of sales people. With the 3DPRINTUK system, I can tweak things and assess the effect on cost and build time, and select what I want rather than what I am being sold.”
One of Jonny’s recent projects is the Monster 917, a stunning half-sized sculpture inspired by the iconic Porsche 917k, which is a maze of tubular aluminium and carbon fibre connected by his own 3D printed joints. Ambrose concludes, “The Monster 917 has taken a lot of work, and the use of 3D printing to produce the joints that hold all the tubes together exemplifies a perfect use of the technology. Creating a sculpture like this is a learning curve. Some of the first 3D printed parts used in the chassis were grey undyed MJF parts as they suited the aluminium tubes. I then used black polished joints when joining the carbon fibre. I knew 3DPRINTUK had the process versatility and post-processing technologies I needed to accommodate these requirements. Each of the male lugs that hold the tubes were initially un-flanged, but as the design went on, I designed them to have a spring-like tension which gripped the tube more firmly. Design tweaks and innovative possibilities that could only really be realised through 3D printing.”
“The combination of capability and expertise at 3DPRINTUK is what works for me. While the automated system is so good, it is re-assuring to know that behind the scenes is a team of experts that are always on hand to advise and optimise outcomes.”